Nitro-V steel represents a compelling material choice for knife makers and enthusiasts alike; What Is Nitro V Steel Comparable To in terms of performance, properties, and applications? This article provides a detailed comparison of Nitro-V with other popular knife steels, guiding you to make informed decisions with the assistance of COMPARE.EDU.VN. Explore similar steel options like AEB-L and 14C28N, material attributes, heat treatment.
1. Introduction to Nitro-V Steel and Its Competitors
Nitro-V steel, a stainless steel developed by New Jersey Steel Baron in collaboration with Buderus Steel, emerged as a modified version of Uddeholm AEB-L, enhanced with nitrogen and vanadium. A close comparison can also be drawn with 14C28N, which was designed as an improved corrosion resistance variant of 13C26, a steel nearly identical to AEB-L but produced by Sandvik. Understanding the origins and compositions of these steels is crucial in determining “what is Nitro V steel comparable to.”
2. Decoding the Composition of Nitro-V Steel
At first glance, Nitro-V mirrors AEB-L closely, sharing similar levels of Carbon, Chromium, and Silicon, with only minor variances in Manganese. The nitrogen content aligns with that of 14C28N, potentially due to production limitations in conventional steelmaking. While vanadium is added, its quantity is minimal, likely insufficient to notably enhance wear resistance or edge retention. Typically, trace amounts of vanadium are used for grain refinement, particularly in low alloy steels. However, stainless steels, rich in chromium, necessitate higher vanadium content for effective grain refinement.
3. Hardness Characteristics of Nitro-V Steel
Nitro-V, akin to other stainless steels, exhibits high hardenability, allowing for air or plate quenching to achieve desired hardness levels. While oil quenching remains an option, plate quenching is preferable for maintaining flatness. For optimal strength, cryogenic processing during heat treatment is recommended.
3.1. Heat Treatment Experiments
Experiments involving austenitizing Nitro-V at temperatures ranging from 1850°F to 2000°F, followed by plate quenching and immediate submersion in liquid nitrogen, revealed that peak hardness is attained at 1950°F and sustained up to 2000°F. Therefore, it is advisable to austenitize at or below 1950°F to avoid compromising strength and toughness due to increased retained austenite at higher temperatures.
3.2. Impact of Cryogenic Processing
Omitting cryogenic processing during heat treatment results in reduced hardness and a lower peak austenitizing temperature. Immediate freezer storage post-quenching is recommended to mitigate retained austenite as much as possible.
3.3. Hardness Comparison with Other Steels
Nitro-V’s peak hardness is comparable to that of AEB-L and 14C28N. AEB-L and Nitro-V both reach approximately 64 Rc, while 14C28N achieves 63.5 Rc, although further austenitizing of 14C28N might reveal its hardness decline point. The peak austenitizing temperature for Nitro-V is slightly lower than that of AEB-L.
4. The Role of Nitrogen in Enhancing Hardness
Nitrogen is frequently incorporated into steel formulations to enhance hardness, corrosion resistance, or both. For instance, 14C28N was engineered with reduced carbon content and increased nitrogen to maintain hardness levels and improve corrosion resistance by increasing chromium. Unlike carbon, nitrogen is less prone to forming nitrides with chromium, thus allowing for improved hardness without compromising corrosion resistance. However, in the case of Nitro-V, the addition of nitrogen did not significantly enhance hardness compared to AEB-L.
5. Chromium and Its Influence on Corrosion Resistance
In stainless steels, the proportion of retained austenite for a given amount of carbon in solution (hardness) is determined by the quantity of chromium in solution (corrosion resistance). The similar peak hardness observed in Nitro-V and AEB-L suggests a comparable amount of chromium in solution. Given that AEB-L and Nitro-V share the same bulk Cr content, increasing Cr in solution in Nitro-V would necessitate a reduction in carbide content, which would negatively impact wear resistance and slicing edge retention.
5.1. Thermo-Calc Analysis
Calculations derived from Thermo-Calc confirm that the chromium content in solution is similar for both steels, particularly when considering the lower austenitizing temperature required for Nitro-V. In contrast, 14C28N exhibits significantly higher chromium in solution, likely contributing to its superior corrosion resistance compared to Nitro-V and AEB-L.
6. The Impact of Nitrogen on Corrosion Resistance
Nitrogen can enhance corrosion resistance, especially against pitting, with its contribution being 16 times that of chromium. Therefore, 0.11% nitrogen is roughly equivalent to 1.75% Cr in terms of pitting resistance. Consequently, Nitro-V may offer slightly better corrosion resistance than AEB-L, depending on the specific environment. 14C28N, with its similar nitrogen content and higher chromium in solution, is expected to outperform Nitro-V in corrosion resistance.
7. Microstructural Analysis
Microscopic examination reveals distinct characteristics among Nitro-V, AEB-L, and 14C28N:
Nitro-V (1950°F austenitize)
AEB-L (1975°F austenitize)
14C28N (1950°F austenitize)
Nitro-V exhibits a very fine microstructure, possibly slightly less refined than AEB-L. Both AEB-L and Nitro-V have similar carbide volumes, approximately 4-6%. 14C28N appears to have somewhat larger carbides but remains significantly finer than many powder metallurgy steels.
8. Optimizing Toughness in Nitro-V Steel
To assess toughness, Nitro-V specimens were austenitized at 1850, 1900, and 1950°F, plate quenched, cryogenically treated, and tempered twice at 350°F. Testing involved averaging results from three unnotched subsize charpy specimens.
8.1. Impact of Austenitizing Temperature on Toughness
The 1850°F austenitizing temperature resulted in reduced toughness compared to 1900 and 1950°F conditions. This may be due to inadequate carbide dissolution or increased retained austenite.
8.2. Effect of Tempering Temperature on Toughness
Specimens austenitized at 1950°F and tempered at 300°F exhibited increased hardness but reduced toughness. Tempering at 450°F led to a decrease in both hardness and toughness, making it a less desirable option.
9. Toughness Comparison with Other Steels
Nitro-V demonstrates excellent toughness, slightly lower than AEB-L but significantly tougher than powder metallurgy stainless steels like M390, Elmax, and S35VN. This makes Nitro-V suitable for knives requiring high toughness.
10. Edge Retention Characteristics
Nitro-V is expected to have similar wear resistance and edge retention to AEB-L, though empirical testing is lacking. The compositions and microstructures of these steels are comparable. AEB-L’s edge retention is similar to that of 52100, lower than higher carbide content stainless steels like 440C, CPM-154, and S30V, but with superior toughness.
11. Comprehensive Comparison Table: Nitro-V vs. AEB-L vs. 14C28N
To provide a clear understanding of the similarities and differences, here’s a detailed comparison in table format.
Feature | Nitro-V | AEB-L | 14C28N |
---|---|---|---|
Composition | Similar to AEB-L with N and V | Basic stainless steel | Modified 13C26 with higher Cr and N |
Hardness (Peak) | ~64 Rc | ~64 Rc | ~63.5 Rc |
Corrosion Resistance | Potentially better than AEB-L | Good | Excellent |
Toughness | Very Good | Slightly better than Nitro-V | Good |
Edge Retention | Similar to AEB-L | Similar to 52100 | Slightly Better than AEB-L |
Microstructure | Very Fine | Very Fine | Fine, slightly larger carbides |
Heat Treatment | 1900-1950°F, Plate Quench, Cryo | Similar, slightly higher austenitizing | Varies based on desired properties |
Nitrogen Content | Similar to 14C28N | Lower | Similar to Nitro-V |
Vanadium Content | Small addition for grain refinement | None | None |
Chromium in Solution | Similar to AEB-L | Similar to Nitro-V | Significantly higher |
Optimal Tempering Temp | 300-350°F | Similar | Varies |
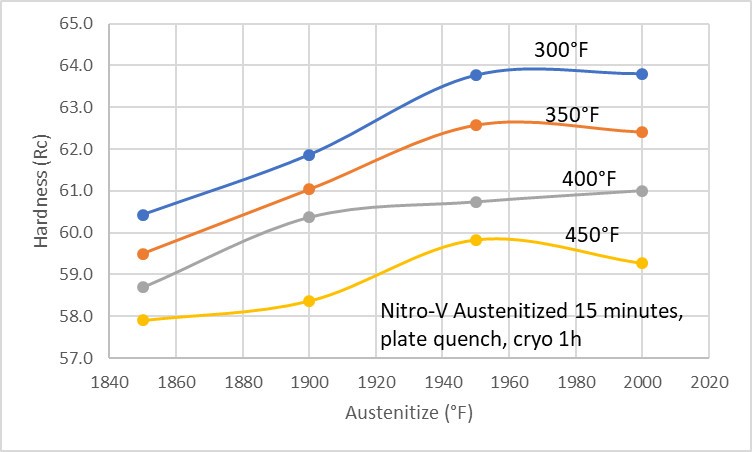
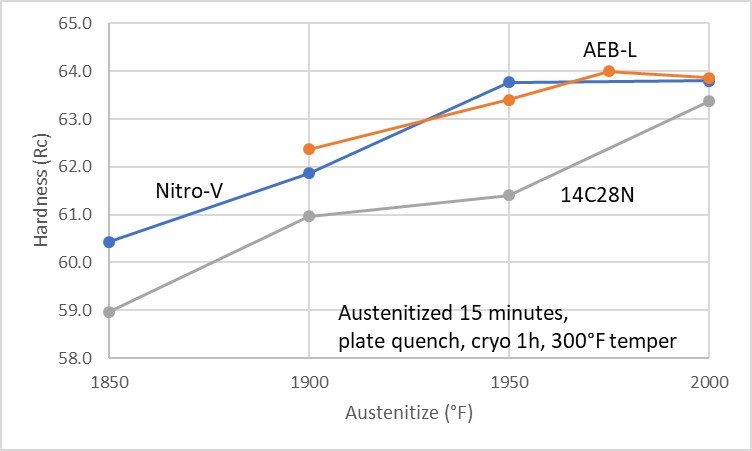
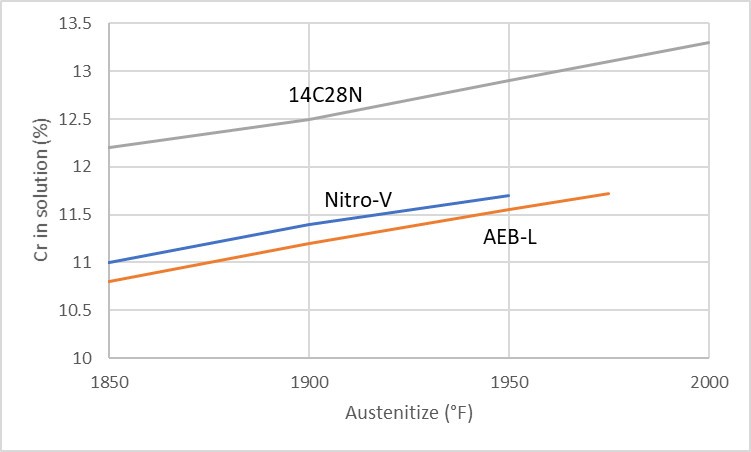
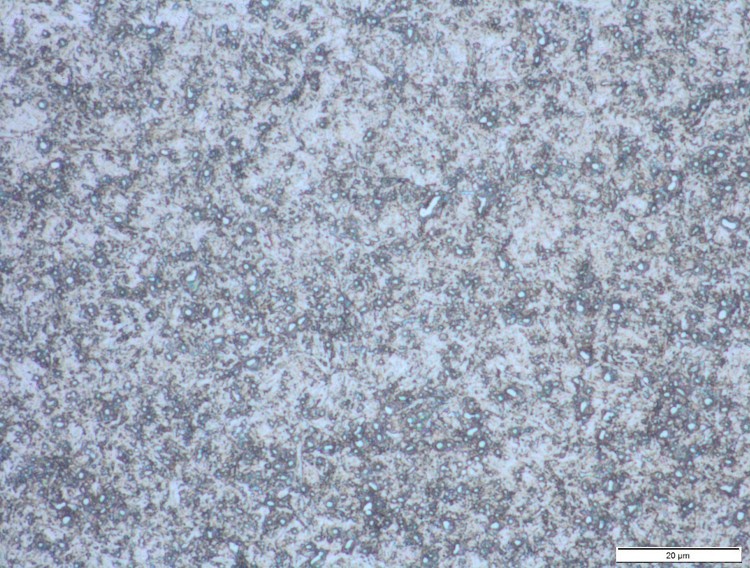
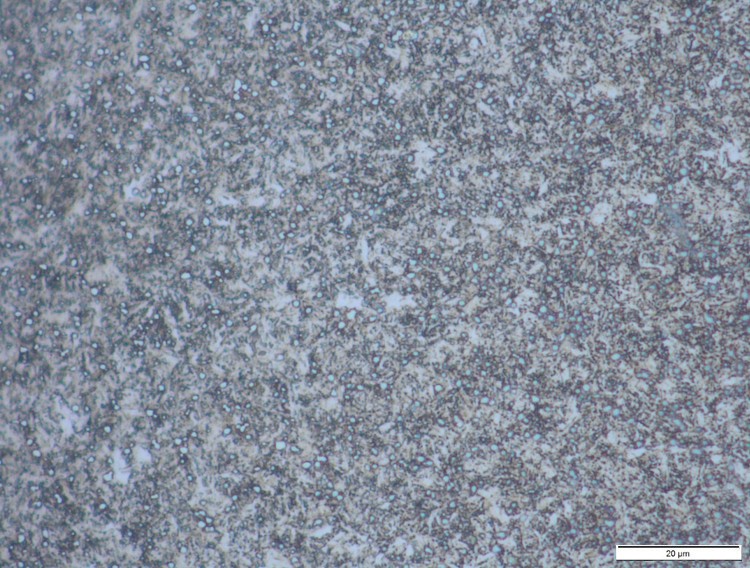
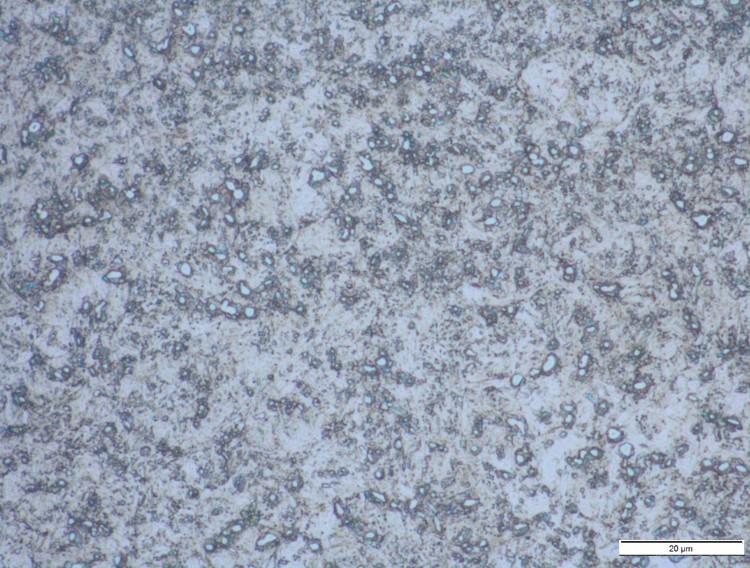
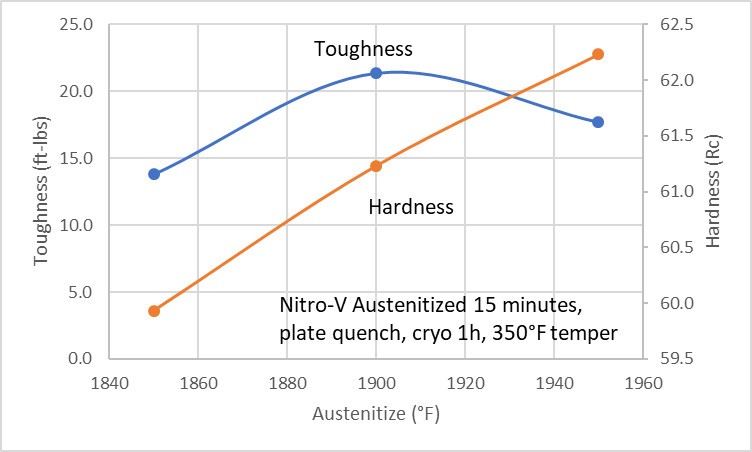
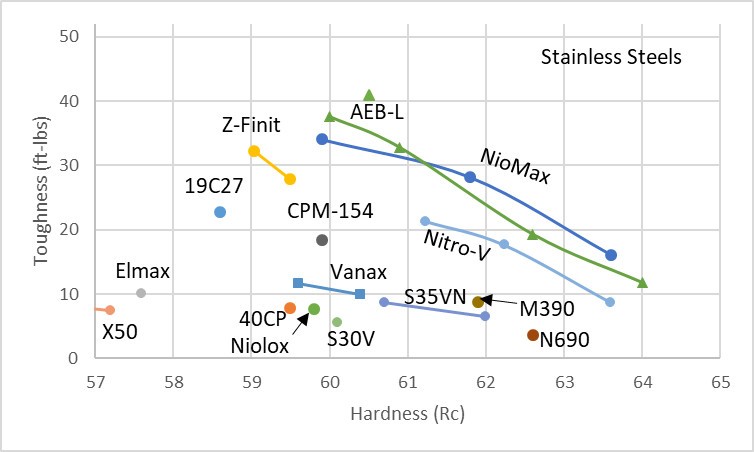
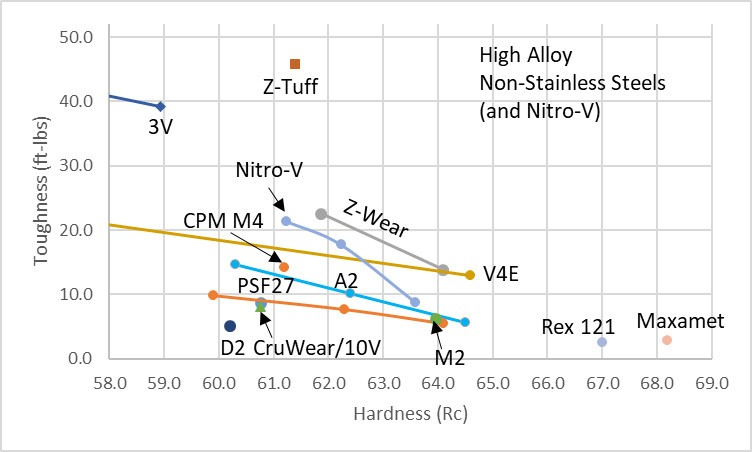
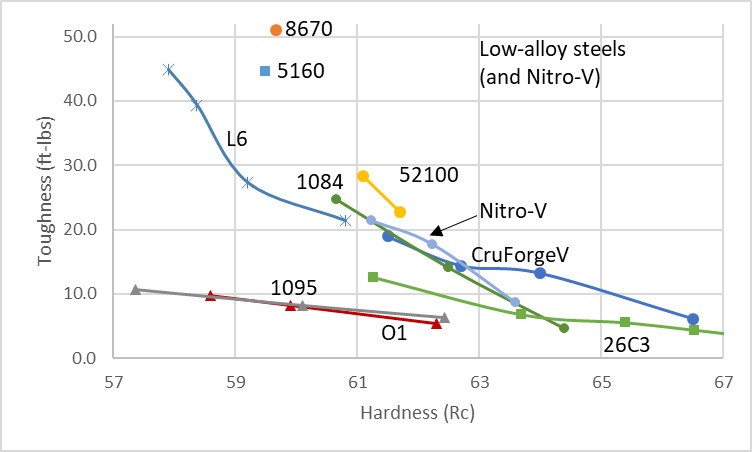
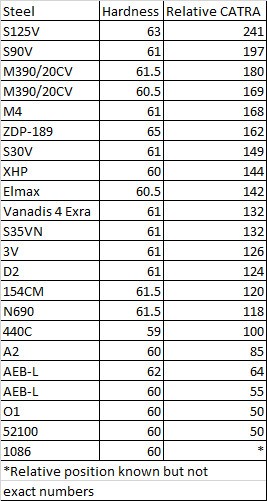
12. Advantages and Disadvantages of Nitro-V Steel
Understanding the pros and cons helps in evaluating “what is Nitro V steel comparable to” and its suitability for specific applications.
12.1. Advantages of Nitro-V Steel
- High Toughness: Superior to many stainless steels, making it suitable for knives that require durability.
- Good Hardness: Achieves high hardness levels with proper heat treatment, ensuring a sharp and lasting edge.
- Fine Microstructure: Contributes to enhanced edge stability and sharpness.
- Potential for Improved Corrosion Resistance: Nitrogen addition may offer better corrosion resistance compared to AEB-L.
12.2. Disadvantages of Nitro-V Steel
- Edge Retention: Lower edge retention compared to high-carbide stainless steels like S30V or CPM-154.
- Vanadium Content: Minimal vanadium may not significantly impact wear resistance.
- Heat Treatment Sensitivity: Requires precise heat treatment to achieve optimal hardness and toughness.
13. Practical Applications of Nitro-V Steel
Nitro-V steel is commonly used in various knife types due to its balance of properties.
13.1. Common Uses
- Everyday Carry (EDC) Knives: Excellent toughness and good corrosion resistance make it ideal for daily use.
- Kitchen Knives: Sharpness and ease of maintenance are valued in kitchen environments.
- Hunting Knives: Toughness ensures durability in field conditions.
- Tactical Knives: Reliable performance under stress.
- Fixed Blade Knives: Strength and toughness provide long-lasting performance.
13.2. Examples of Knives Using Nitro-V Steel
- Benchmade: Known for using Nitro-V in their EDC and tactical knives.
- Spyderco: Offers several models featuring Nitro-V steel for its balanced properties.
- Zero Tolerance (ZT): Uses Nitro-V in select knives for its toughness and corrosion resistance.
- Custom Knife Makers: Many independent makers choose Nitro-V for its desirable qualities and ease of heat treatment.
14. Expert Opinions on Nitro-V Steel
Feedback from knife makers and users provides practical insights into Nitro-V steel’s performance.
14.1. Knife Makers’ Perspectives
- Heat Treatment: Generally easy to work with, achieving consistent results with proper heat treatment protocols.
- Workability: Good machinability and ease of grinding.
- Performance: Praised for its balanced properties, making it versatile for different knife types.
14.2. User Reviews
- Sharpness: Users appreciate its ability to take and hold a sharp edge.
- Durability: Noted for its toughness and resistance to chipping and breaking.
- Corrosion Resistance: Performs well in various environments, requiring minimal maintenance.
15. The Science Behind Nitro-V Steel
Delving into the metallurgy offers a deeper understanding of “what is Nitro V steel comparable to” from a scientific standpoint.
15.1. Chemical Composition Breakdown
Understanding the elemental composition helps to predict material behavior.
- Carbon (C): Contributes to hardness and edge retention.
- Chromium (Cr): Enhances corrosion resistance.
- Nitrogen (N): Improves hardness and corrosion resistance.
- Vanadium (V): Promotes grain refinement.
- Manganese (Mn): Improves hardenability.
- Silicon (Si): Enhances strength.
15.2. Role of Alloying Elements
Each element plays a crucial role in determining the final properties of Nitro-V steel.
- Carbon vs. Nitrogen: Nitrogen is added to compensate for carbon, improving hardness without sacrificing corrosion resistance.
- Chromium’s Influence: High chromium content ensures excellent corrosion resistance.
- Vanadium’s Grain Refinement: While present in small quantities, vanadium contributes to grain refinement.
16. Heat Treatment Protocols for Nitro-V Steel
Proper heat treatment is essential to maximizing the performance of Nitro-V steel.
16.1. Recommended Heat Treatment Steps
- Preheating: Gradually heat the steel to reduce thermal stress.
- Austenitizing: Heat to the recommended temperature (1900-1950°F) to dissolve carbides and achieve desired hardness.
- Quenching: Rapidly cool the steel using plate quenching to form martensite.
- Cryogenic Treatment: Submerge in liquid nitrogen to reduce retained austenite.
- Tempering: Heat to the recommended tempering temperature (300-350°F) to reduce brittleness and increase toughness.
16.2. Common Mistakes to Avoid
- Overheating: Can lead to excessive retained austenite and reduced toughness.
- Insufficient Quenching: Results in lower hardness and poor performance.
- Improper Tempering: Can cause embrittlement or reduce hardness.
17. Corrosion Resistance: A Detailed Examination
Understanding corrosion resistance is key to appreciating “what is Nitro V steel comparable to” in various environments.
17.1. Factors Affecting Corrosion Resistance
- Chromium Content: High chromium content is crucial for forming a protective oxide layer.
- Nitrogen Content: Nitrogen enhances resistance to pitting corrosion.
- Environmental Factors: Exposure to salt water, acids, and other corrosive agents can accelerate corrosion.
17.2. Comparing Corrosion Resistance with Other Steels
- Nitro-V vs. AEB-L: Nitro-V may offer slightly better corrosion resistance due to nitrogen addition.
- Nitro-V vs. 14C28N: 14C28N generally provides superior corrosion resistance due to higher chromium content.
18. Edge Retention: How Nitro-V Stacks Up
Edge retention is a critical factor in knife performance and user satisfaction.
18.1. Factors Influencing Edge Retention
- Hardness: Higher hardness generally leads to better edge retention.
- Carbide Volume: Higher carbide volume enhances wear resistance and edge retention.
- Microstructure: Fine microstructure contributes to edge stability and sharpness.
18.2. Edge Retention Comparison
- Nitro-V vs. AEB-L: Expected to have similar edge retention due to similar compositions and microstructures.
- Nitro-V vs. S30V: S30V typically offers better edge retention due to higher carbide content.
19. User Experiences and Real-World Testing
Gathering feedback from users and test results provides a comprehensive understanding of Nitro-V steel’s performance.
19.1. User Testimonials
- Everyday Use: Users report good sharpness, durability, and ease of maintenance for EDC knives.
- Professional Use: Chefs and hunters appreciate the balance of sharpness and toughness for kitchen and hunting knives.
- Outdoor Activities: Campers and hikers value the corrosion resistance and toughness for survival knives.
19.2. Comparative Testing Data
- Edge Retention Tests: Comparing edge retention of Nitro-V with other steels in controlled environments.
- Corrosion Resistance Tests: Evaluating corrosion resistance in salt spray and other corrosive environments.
- Toughness Tests: Measuring impact resistance and fracture toughness.
20. Future Trends in Knife Steel Technology
Knife steel technology continues to evolve, with new materials and processes emerging.
20.1. Emerging Steel Alloys
- CPM Cru-Wear: High toughness and good wear resistance.
- Vanax: Excellent corrosion resistance and high hardness.
- CPM MagnaCut: Balanced properties with exceptional toughness and corrosion resistance.
20.2. Advanced Heat Treatment Techniques
- Vacuum Heat Treatment: Provides precise control over heating and cooling rates.
- Deep Cryogenic Treatment (DCT): Enhances hardness and wear resistance.
- Martensitic Transformation: Optimizing martensitic transformation for improved properties.
21. Maintaining and Caring for Nitro-V Steel Knives
Proper maintenance ensures long-lasting performance and durability.
21.1. Cleaning and Sharpening Tips
- Cleaning: Wash with mild soap and water, dry thoroughly.
- Sharpening: Use appropriate sharpening tools and techniques to maintain a sharp edge.
- Oiling: Apply a thin coat of oil to protect against corrosion.
21.2. Storage Recommendations
- Dry Environment: Store in a dry place to prevent corrosion.
- Sheath/Case: Use a sheath or case to protect the blade.
22. Addressing Common Misconceptions about Nitro-V Steel
Clearing up misconceptions ensures informed decisions and realistic expectations.
22.1. Myth vs. Reality
- Myth: Nitro-V is as wear-resistant as high-carbide steels.
- Reality: Nitro-V offers good wear resistance but is not comparable to high-carbide steels like S30V.
- Myth: Nitro-V is completely rust-proof.
- Reality: Nitro-V offers excellent corrosion resistance but can still corrode under extreme conditions.
22.2. Accurate Expectations
- Balanced Properties: Nitro-V excels in providing a balance of toughness, hardness, and corrosion resistance.
- Maintenance: Requires regular cleaning and sharpening to maintain optimal performance.
23. Case Studies: Successful Applications of Nitro-V Steel
Examining real-world examples illustrates the effectiveness of Nitro-V steel in different applications.
23.1. Knives in Culinary Arts
- Chef’s Knives: Providing sharpness and durability for professional chefs.
- Paring Knives: Offering precision and control for detailed tasks.
23.2. Knives for Outdoor and Survival
- Hunting Knives: Delivering toughness and edge retention for field dressing game.
- Survival Knives: Providing reliability and durability in challenging conditions.
24. Frequently Asked Questions (FAQs) About Nitro-V Steel
Addressing common questions helps clarify key points and provide practical guidance.
24.1. Top 10 FAQs
-
What is Nitro-V steel?
- Nitro-V is a stainless steel developed as a modified version of AEB-L, enhanced with nitrogen and vanadium.
-
How does Nitro-V compare to AEB-L?
- Nitro-V is very similar to AEB-L, with potential improvements in corrosion resistance due to nitrogen addition.
-
Is Nitro-V better than 14C28N?
- 14C28N typically offers better corrosion resistance, while Nitro-V may provide slightly better toughness.
-
What is the ideal heat treatment for Nitro-V steel?
- Austenitizing at 1900-1950°F, followed by plate quenching, cryogenic treatment, and tempering at 300-350°F.
-
What are the common uses for Nitro-V steel knives?
- EDC knives, kitchen knives, hunting knives, and tactical knives.
-
How do I maintain a Nitro-V steel knife?
- Clean with mild soap and water, dry thoroughly, sharpen regularly, and apply a thin coat of oil.
-
Does Nitro-V steel rust?
- Nitro-V offers excellent corrosion resistance but can still corrode under extreme conditions.
-
What makes Nitro-V steel tough?
- The fine microstructure and optimized heat treatment contribute to its high toughness.
-
How does the edge retention of Nitro-V compare to other steels?
- It is similar to AEB-L but lower than high-carbide steels like S30V.
-
Is Nitro-V a good choice for a survival knife?
- Yes, its toughness, corrosion resistance, and ease of maintenance make it a reliable choice for survival knives.
25. Conclusion: Making an Informed Decision
Nitro-V steel stands out as a balanced option for knife enthusiasts seeking a blend of toughness, corrosion resistance, and ease of maintenance. While it may not surpass high-carbide steels in edge retention or offer the absolute best corrosion resistance, its overall performance makes it a versatile choice for various applications.
Whether you are a knife maker, a professional chef, or an outdoor enthusiast, understanding the properties and characteristics of Nitro-V steel will help you make an informed decision. For more detailed comparisons and insights, visit COMPARE.EDU.VN, where you can explore a wide range of steel options and find the perfect material for your needs.
Call to Action
Ready to make an informed decision about your next knife steel? Visit COMPARE.EDU.VN today to explore detailed comparisons, user reviews, and expert opinions on Nitro-V steel and other top contenders. Don’t settle for less – discover the perfect steel for your needs and elevate your cutting experience.
Address: 333 Comparison Plaza, Choice City, CA 90210, United States
WhatsApp: +1 (626) 555-9090
Website: compare.edu.vn