Optical comparators are indispensable tools in manufacturing for quality control, but What Is An Optical Comparator Used For specifically? This article from COMPARE.EDU.VN delves into the multifaceted applications of optical comparators, exploring their functionality, benefits, and how they compare to digital alternatives, providing insight into their continued relevance and optical measurement techniques. This comparison ensures you understand the importance of optical inspection and profile projection.
1. Understanding Optical Comparators
Optical comparators, also known as profile projectors, are instruments used in the manufacturing sector for meticulous inspection and precise measurement of manufactured parts. These devices operate on basic optical principles. Illumination, lenses, and mirrors work in concert to project a magnified silhouette of the part onto a screen, offering a detailed view for comparison against specified tolerances.
Optical comparators meticulously check dimensional accuracy and spot surface defects, such as scratches or indentations. They facilitate non-contact measurements and observations, reducing part handling while enhancing close inspection.
These comparators come in two main setups: horizontal and vertical.
- Horizontal Comparators: Ideal for parts held in place, horizontal comparators project light horizontally, allowing a side view of the part. They are best used for items like fixed screws or castings held in a vise.
- Vertical Comparators: Designed for flat components, vertical comparators project light vertically, offering a top-down view. They suit gaskets well and are ideal for flexible materials needing support from a flat surface for measurement accuracy.
Both types of optical comparators play crucial roles in quality control across industries like automotive, aerospace, medical manufacturing, and scientific research.
2. The Operational Mechanics of an Optical Comparator
Since their inception in the 1920s, optical comparators have maintained their fundamental design, proof of the enduring effectiveness of their underlying optical technology. These machines share similarities with overhead projectors, commonly used in educational settings. Light passes through a stage, then through a series of lenses and mirrors, projecting an enlarged silhouette of the object onto a screen.
An optical comparator works by securing a part on a stage, then shining a light source onto it to create a shadow image. Lenses magnify this shadow, which is then reflected by mirrors onto a screen positioned at a set distance, facilitating precise measurement.
Variations in optical comparators depend on the size and magnification of the projected image, factors determined by the device’s optics and screen dimensions. Screen sizes range from 12 to 36 inches, with larger sizes available in larger enclosures to maintain image quality without distortion.
Measuring processes also vary among optical comparators. The three primary methods include:
- Silhouette Measurement: Projects an image silhouette onto a screen for direct measurement, using the known magnification to achieve accuracy.
- Point Comparison: Compares the image silhouette to preset points on a screen, where the stage is adjusted to align the part with these points, measuring the necessary movement.
- Software Analysis: Utilizes digital software to analyze and measure the image electronically, commonly found in digital optical comparators.
Traditional optical comparators typically employ the first two methods, while digital models use software for electronic processing.
3. Traditional Optical Comparator Operation: A Step-by-Step Guide
Operating a traditional optical comparator involves a straightforward process:
- Placement: Power on the comparator and place the part on the staging area.
- Alignment: Project the part’s image onto the screen and place an overlay, known as a template or Mylar, on the screen. This overlay, scaled to match the comparator’s magnification, aligns with the part’s image.
- Comparison: Compare the image against the overlay to identify discrepancies and assess if the part meets tolerance standards.
This method, used widely in traditional optical comparators, may also involve grid or concentric circle overlays for more detailed measurements, or point comparison for aligning and measuring against preset points.
4. Disadvantages of Traditional Optical Comparators
While straightforward, traditional optical comparators have inherent limitations:
- Complexity Constraints: They struggle with increasingly complex parts requiring multi-angle analysis.
- Accuracy Concerns: Despite their potential for accurate measurements, modern parts demand tighter tolerances, reducing the margin for error in manual measurements.
- Labor Intensity: Traditional comparators assess one part at a time, posing challenges for large-scale inspections.
- 2D Limitations: Projecting only 2D images restricts comprehensive, multi-dimensional analysis.
These constraints limit traditional optical comparators in handling repetitive tasks and complex parts, making them unsuitable for large-scale, complex analysis.
5. Digital vs. Traditional Optical Comparators: A Comparative Analysis
Digital optical comparators address the shortfalls of their traditional counterparts. While manual comparators are valuable for small quantities, digital models provide the automation needed for complex parts and large-scale manufacturing.
Digital optical comparators offer:
- Automation: Software and cameras automate analysis and measurement, accelerating the process.
- 3D Capability: Multiple lighting techniques and 3D inspection methods enable comprehensive dimensional analysis.
- Quantity Management: Automated systems can analyze multiple parts without human intervention.
- Accuracy: Removing human error improves measurement accuracy, essential for modern technologies.
These improvements boost optical measurement accuracy and reduce labor demands.
6. Traditional Optical Comparators vs. Digital: Practical Considerations
Traditional optical comparators pose disadvantages in terms of usability and results:
- Limited Quantifiable Data: Subjective measurements make it hard to provide detailed, quantifiable data on deviations.
- Inflexibility: 2D image projection limits analysis of complex parts, requiring extensive manual adjustments and multiple overlays.
- Reduced Accuracy: Achieving accuracy requires well-trained operators, and manual operations are prone to human error.
- High Costs: Overlays are expensive, and significant labor inputs increase operational costs, especially for complex parts.
Overall, traditional optical comparators demand extensive training and high labor input. While sufficient for simple parts in small operations, the manufacturing industry’s rapid growth and complexity necessitate more advanced tools.
7. Streamlining Inspection: The Digital Optical Comparator Advantage
Digital optical comparators streamline inspection processes for faster, easier operation. These systems combine measurement and analysis tools with existing comparator technology, referencing CAD drawings, laser measurements, and advanced software.
For operators, the process simplifies to placing the part on the staging area. The digital comparator then handles alignment and comparison automatically, providing pass/fail results with supporting analytical data.
Digital comparators also offer:
- Fast Automation: Software and cameras automate part analysis and measurement, aligning parts with CAD drawings in seconds.
- 3D Capability: Multiple lighting techniques and lasers allow comprehensive dimensional analysis with minimal interference.
- Improved Accuracy: Automatic measurements eliminate human error, providing detailed documentation with statistics and pass/fail results.
Even with automation, the VisionGauge® software provides an intuitive interface for manual measurements, allowing operators to load CAD files and inspection routines quickly with barcode readers, with stages and overlays controlled by industrial-grade joysticks. Both modes ensure highly accurate results and complete documentation.
8. Applications of Digital Optical Comparators Across Industries
Digital optical comparators find use across diverse industries for applications like:
Industry | Application |
---|---|
Aerospace | Inspecting turbine blades for precise dimensions and surface integrity, verifying the accuracy of machined components used in aircraft engines, ensuring that all parts meet stringent safety standards and performance criteria. |
Automotive | Measuring engine parts to ensure they meet performance specifications, checking the dimensions of stamped metal components for body construction, guaranteeing the precision of fuel injectors and other critical components to improve efficiency and reduce emissions. |
Medical Device | Examining surgical instruments for defects, ensuring that implants meet size and shape requirements, verifying the precision of micro-components used in medical devices for accurate functionality and patient safety. |
Electronics | Inspecting circuit boards for proper component placement, verifying the dimensions of connectors and terminals, ensuring the quality and accuracy of semiconductor components to maintain the performance and reliability of electronic devices. |
Manufacturing | Measuring precision-machined parts for dimensional accuracy, inspecting molds and dies for wear and damage, verifying the dimensions and quality of fasteners and fittings to ensure proper assembly and functionality. |
Scientific Research | Analyzing the structure and dimensions of microscopic specimens, measuring the accuracy of laboratory equipment components, ensuring the precision of experimental setups to obtain reliable and accurate data for scientific studies. |
Defense | Inspecting firearms components for proper fit and function, verifying the dimensions of ammunition components, ensuring the accuracy of guidance systems and other critical defense equipment to maintain reliability and effectiveness in defense applications. |
Quality Control | Conducting thorough inspections of incoming materials to ensure they meet specified quality standards, performing in-process inspections to identify and correct defects during manufacturing, verifying the quality of finished products before they are shipped to customers to maintain customer satisfaction. |
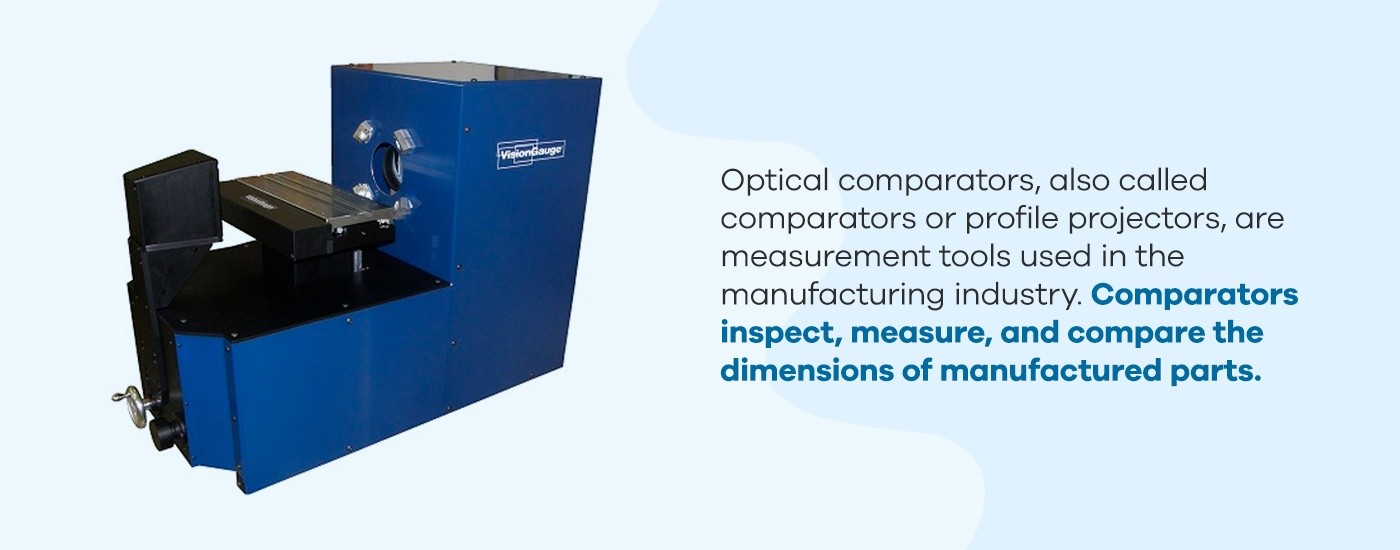
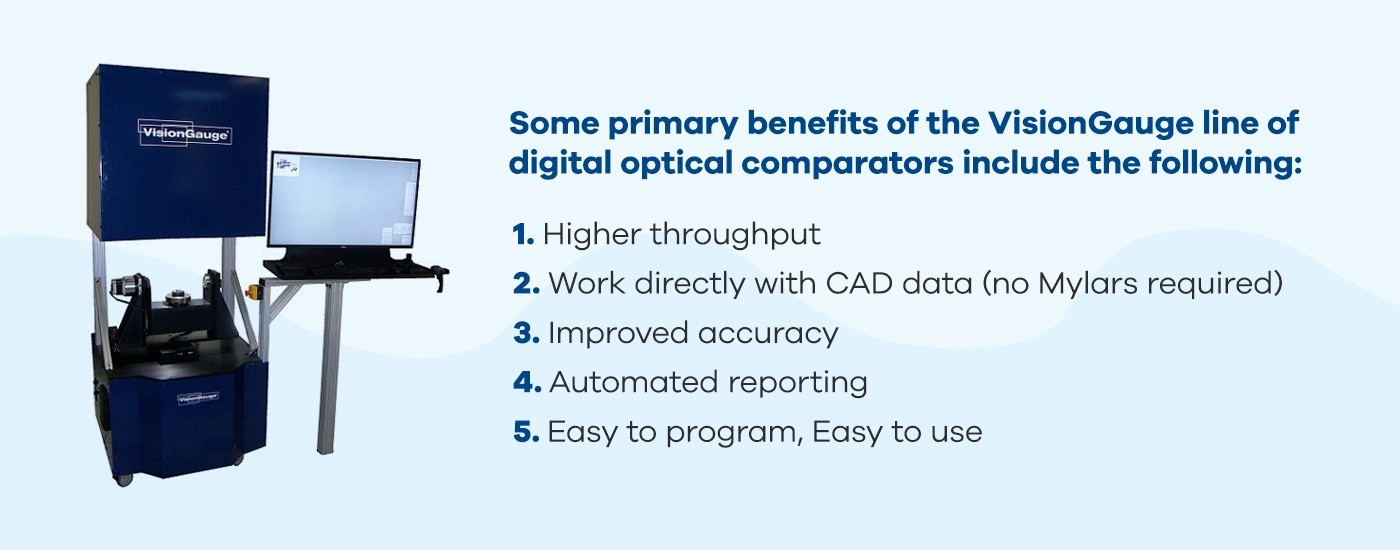
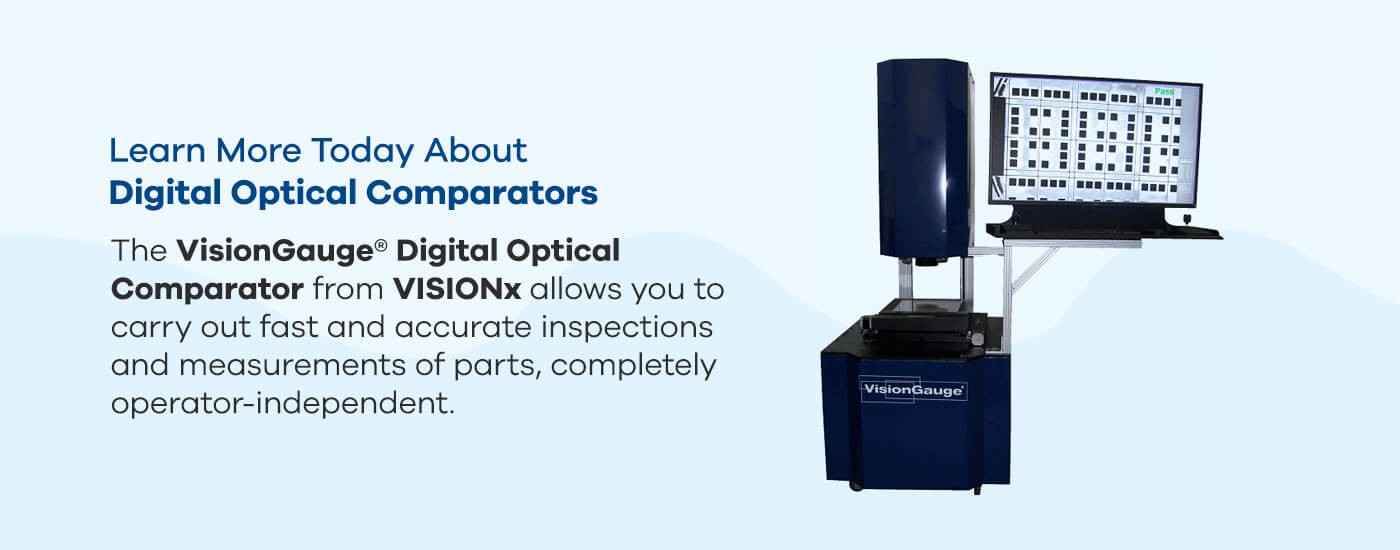
Digital optical comparators have many applications in addition to those listed above.
9. Maximize Your Quality Control with Advanced Optical Comparators
Do you want to learn more?
Using an optical comparator doesn’t need to require extensive training or massive labor inputs. Simplify your optical inspection with VISIONx, Inc’s VisionGauge® Digital Optical Comparator. Our digital optical comparator is an advanced optical analysis tool that maximizes the function of optical comparator technology. They are extremely precise yet easy to use, delivering fast, high-quality results. They allow you to carry out fast and accurate inspections and measurements of parts, completely operator-independent.
VISIONx, Inc. has multiple optical comparators for sale. Each model presents competitive advantages and includes VisionGauge® software with a wide range of applicability. On top of our optical comparators, VISIONx, Inc. develops, sells, and supports software, systems, and hardware for other automated imaging, visual inspection, and measurement solutions. With powerful and easy-to-use products, you can rely on VISIONx, Inc. for custom or standard solutions in various industries — from aerospace and automotive to electronic and medical device manufacturing.
10. Seeking Comprehensive Comparisons? Discover COMPARE.EDU.VN
Determining the ideal tool for your manufacturing needs can be daunting given the array of options. Optical comparators, whether traditional or digital, offer distinct advantages depending on the complexity and scale of your operations. The key lies in understanding your specific requirements and aligning them with the capabilities of available technologies.
Are you facing challenges in comparing different options objectively? Do you lack the detailed, reliable information needed to make the right decisions? Are you overwhelmed by too much information and unsure where to focus?
COMPARE.EDU.VN is here to help. We provide detailed and objective comparisons across a range of products, services, and ideas. Our platform clearly outlines the pros and cons of each option, comparing features, specifications, prices, and other crucial factors. You’ll find reviews and feedback from users and experts, enabling you to identify the best choice for your needs and budget.
Visit COMPARE.EDU.VN today to explore comprehensive comparisons and make informed decisions. Let us help you find the perfect solution with clear, reliable, and objective information. Contact us at 333 Comparison Plaza, Choice City, CA 90210, United States. Reach out via Whatsapp at +1 (626) 555-9090 or visit our website at COMPARE.EDU.VN for more information.
11. Frequently Asked Questions (FAQ) about Optical Comparators
- What is the basic principle behind an optical comparator?
- An optical comparator projects a magnified image of a part onto a screen, enabling precise measurements and comparisons against specified tolerances.
- What are the main differences between horizontal and vertical optical comparators?
- Horizontal comparators project a side view and are best for fixed parts, while vertical comparators offer a top-down view, ideal for flat components.
- How does a traditional optical comparator work?
- It involves placing a part on a stage, projecting its magnified image onto a screen, and manually comparing it against an overlay or template.
- What are the limitations of using traditional optical comparators?
- Limitations include difficulty with complex parts, less accuracy compared to digital systems, labor-intensive processes, and 2D image projection.
- What advantages do digital optical comparators offer over traditional models?
- Digital models offer automation, 3D capability, quantity management, and improved accuracy by removing human error.
- How do digital optical comparators automate the inspection process?
- They use software and cameras to analyze parts, automatically align them with CAD drawings, and provide pass/fail results with detailed data.
- In what industries are digital optical comparators commonly used?
- Common industries include aerospace, automotive, medical device manufacturing, electronics, and scientific research.
- How does the VisionGauge® software enhance the functionality of digital optical comparators?
- It provides an intuitive interface for both automated and manual operation, allowing users to quickly load part CAD files and inspection routines.
- What types of measurements can be performed using an optical comparator?
- Optical comparators can perform silhouette measurements, point comparisons, and software analysis for both 2D and 3D dimensions.
- How can COMPARE.EDU.VN help in choosing the right optical comparator?
- compare.edu.vn offers detailed comparisons, outlines pros and cons, and provides reviews from users and experts to help you make an informed decision based on your specific needs and budget.