Tungsten versus titanium: Understanding their strength is crucial in material selection across various industries. At COMPARE.EDU.VN, we analyze the properties of these metals, offering a comprehensive comparison of their tensile strength, compressive strength, yield strength, and impact resistance. Discover which metal is best suited for your specific needs with insights into their hardness and durability.
1. Understanding Metal Strength: An Introduction
When evaluating materials for engineering, manufacturing, or construction, strength is a critical consideration. However, defining “strength” in metals isn’t straightforward. It encompasses different characteristics that describe how a metal responds to various types of stress. Understanding these different types of strength is crucial before comparing materials like tungsten and titanium. These include tensile strength, compressive strength, yield strength, and impact strength.
2. Defining the Types of Metal Strength
2.1. Tensile Strength: Resistance to Pulling
Tensile strength measures a material’s ability to withstand being pulled apart. It is quantified by the amount of force required to cause a material to stretch or break under tension. A metal with high tensile strength can withstand significant pulling forces without deforming or fracturing. This property is vital in applications where the material is subjected to stretching or pulling, such as cables, ropes, and structural components.
2.2. Compressive Strength: Resistance to Squeezing
Compressive strength, in contrast, describes a material’s ability to withstand forces that compress or squeeze it. It measures the amount of pressure a material can endure before it deforms permanently or fractures under compression. This property is essential in applications where the material is subjected to crushing forces, such as pillars, supports, and building foundations. The Mohs Hardness Test is a common method for assessing compressive strength, ranking minerals on a scale from 1 (softest) to 10 (hardest).
2.3. Yield Strength: Resistance to Permanent Deformation
Yield strength is the point at which a material begins to deform permanently. Up to the yield strength, the material will return to its original shape when the stress is removed. Exceeding the yield strength results in permanent deformation. It’s determined through a bend test to see how much stress it requires to exceed the material’s yield point, or the point at which the material will not return to its original shape upon removal of the stress. This is a critical parameter in designing structures and components that must maintain their shape and function under load.
2.4. Impact Strength: Resistance to Sudden Blows
Impact strength measures a material’s ability to withstand a sudden blow or impact without fracturing. It indicates how much energy a material can absorb before it fails under impact. This property is crucial in applications where the material is likely to experience sudden forces, such as automotive parts, protective gear, and aerospace components. The higher the impact strength, the better the material can resist fracturing or shattering upon impact.
3. Comparing Strong Metals: A General Overview
Given that strength is a multifaceted property, identifying a single “strongest metal” is an oversimplification. Instead, several metals exhibit remarkable strength characteristics, each excelling in different aspects. Let’s examine some of the strongest metals on Earth, focusing on their unique properties and applications. It is important to avoid ranking the metals, but rather focusing on their respective strengths.
4. The Strength of Chromium
Chromium is a hard, brittle, steel-gray transition metal known for its exceptional hardness and corrosion resistance. Rated 8.5 on the Mohs Hardness Scale, chromium ranks among the hardest metals, surpassed only by boron (9.5) and diamond (10). Its high hardness makes it ideal for applications requiring wear resistance, such as coatings, alloys, and cutting tools.
5. The Strength of Inconel
Inconel represents a family of nickel-based superalloys renowned for their ability to maintain strength and resist corrosion at extremely high temperatures. Inconel alloys exhibit high tensile strength, ranging from 103 to 160 ksi, compared to stainless steel’s 73.2 ksi. These alloys are favored in aerospace, chemical processing, and power generation applications where materials are exposed to extreme heat and corrosive environments.
6. The Strength of Stainless Steel
Stainless steel is an alloy of iron that is highly regarded for its resistance to rust and corrosion. The strength of stainless steel varies significantly depending on its specific composition. Grade 304 stainless steel, for example, has a tensile strength of up to 621 MPa or 90 KSI. Stainless steel is used in a wide range of applications, including construction, kitchenware, medical devices, and automotive components.
7. The Strength of Titanium
Titanium is an elemental metal that stands out with an extremely high melting point. It boasts a notably high strength-to-weight ratio, making it an ideal metal for applications where weight must be minimized while maintaining maximum strength. Its tensile strength, combined with its low density, makes it a popular choice in aerospace, medical implants, and sporting equipment.
8. The Strength of Tool Steel
Tool steel is a carbon alloy steel specifically designed for manufacturing tools. Its defining characteristics include high hardness, abrasion resistance, and the ability to retain its shape and cutting edge at high temperatures. The ultimate tensile strength of A2 tool steel can reach upwards of 1860 MPa. It is commonly used in making cutting tools, dies, molds, and other industrial applications.
9. The Strength of Tungsten
Tungsten is a naturally occurring metal with exceptional strength and a high melting point. It boasts a tensile strength of approximately 142,000 psi. However, tungsten is brittle and prone to shattering upon impact. With a rating of 9 on the Mohs scale of hardness, it is one of the hardest metals. It’s used in light bulb filaments, welding electrodes, and high-density applications.
10. Tungsten vs Titanium: A Detailed Comparison
Comparing tungsten and titanium highlights the importance of considering multiple strength properties. While tungsten boasts the highest tensile strength among natural metals (142,000 psi), it is brittle and susceptible to fracturing under impact. In contrast, titanium offers a lower tensile strength (63,000 psi) but possesses a significantly higher strength-to-weight ratio and superior impact resistance.
Caption: A visual comparison of Tungsten and Titanium, highlighting their different strengths and applications.
10.1. Strength-to-Weight Ratio
Titanium outperforms tungsten in terms of strength-to-weight ratio. This is because titanium is significantly less dense than tungsten. For applications where weight is a critical factor, titanium is the preferred choice.
10.2. Compressive Strength
Tungsten scores higher than titanium on the Mohs scale of hardness, indicating that it has better compressive strength. This makes tungsten suitable for applications where the material is subjected to high compressive forces.
10.3. Impact Resistance
Titanium exhibits superior impact resistance compared to tungsten. Tungsten is brittle and tends to shatter upon impact, whereas titanium can absorb more energy without fracturing.
10.4. Applications
- Tungsten: Due to its high melting point and strength, tungsten is used in applications such as light bulb filaments, welding electrodes, and high-temperature alloys.
- Titanium: With its high strength-to-weight ratio and corrosion resistance, titanium is used in aerospace components, medical implants, and sporting equipment.
It’s evident that directly comparing tungsten and titanium is complex due to their differing strengths and weaknesses. The choice between the two depends heavily on the specific application requirements.
11. The Importance of Material Selection
Selecting the right material for a given application requires careful consideration of its properties and the specific demands of the environment in which it will be used. Factors such as tensile strength, compressive strength, yield strength, impact resistance, weight, corrosion resistance, and temperature resistance must be evaluated to ensure optimal performance and longevity.
12. Other Notable Metal Comparisons
12.1. Chromium vs. Inconel
Chromium excels in hardness and wear resistance, making it suitable for coatings and cutting tools. Inconel, on the other hand, offers superior high-temperature strength and corrosion resistance, making it ideal for aerospace and chemical processing applications.
12.2. Titanium vs. Steel
Titanium boasts a higher strength-to-weight ratio and superior corrosion resistance compared to steel. However, steel is generally more cost-effective and offers higher tensile strength in certain grades.
12.3. Tungsten vs. Stainless Steel
Tungsten provides exceptional hardness and high-temperature strength, while stainless steel offers excellent corrosion resistance and ductility. The choice between the two depends on the specific application requirements.
13. Factors Affecting Metal Strength
Several factors can influence the strength of a metal, including:
13.1. Alloying
Alloying involves combining two or more metals to create a new material with enhanced properties. Alloying can significantly improve the strength, hardness, corrosion resistance, and other characteristics of metals.
13.2. Heat Treatment
Heat treatment involves subjecting a metal to controlled heating and cooling cycles to alter its microstructure and mechanical properties. Heat treatment can be used to increase the strength, hardness, ductility, and toughness of metals.
13.3. Cold Working
Cold working involves deforming a metal at room temperature to increase its strength and hardness. Cold working can also improve the surface finish and dimensional accuracy of metals.
13.4. Grain Size
The grain size of a metal refers to the average size of the individual crystals within its microstructure. Metals with smaller grain sizes generally exhibit higher strength and toughness compared to those with larger grain sizes.
14. Future Trends in Metal Strength Research
Research into new materials and processing techniques continues to push the boundaries of metal strength. Some promising areas of research include:
14.1. Nanomaterials
Nanomaterials are materials with at least one dimension in the nanometer scale (1-100 nanometers). Nanomaterials can exhibit exceptional strength and other properties due to their unique microstructure and quantum mechanical effects.
14.2. High-Entropy Alloys
High-entropy alloys (HEAs) are alloys containing five or more elements in equal or near-equal proportions. HEAs often exhibit excellent strength, ductility, and corrosion resistance due to their complex microstructure and sluggish diffusion kinetics.
14.3. Additive Manufacturing
Additive manufacturing, also known as 3D printing, allows for the creation of complex geometries and microstructures that are not possible with traditional manufacturing techniques. Additive manufacturing can be used to create metals with tailored strength properties and improved performance.
15. Real-World Applications and Case Studies
15.1. Aerospace Industry
In the aerospace industry, titanium alloys are widely used in aircraft structures and engine components due to their high strength-to-weight ratio and corrosion resistance. Tungsten alloys are used in high-temperature applications such as rocket nozzles and turbine blades.
15.2. Medical Industry
Titanium and its alloys are commonly used in medical implants due to their biocompatibility, corrosion resistance, and strength. Stainless steel is used in surgical instruments and other medical devices.
15.3. Automotive Industry
High-strength steels are used in automotive structures to improve safety and fuel efficiency. Aluminum alloys and composite materials are also used to reduce weight and improve performance.
15.4. Construction Industry
Steel is the primary material used in the construction of buildings, bridges, and other structures due to its strength, durability, and cost-effectiveness. Concrete is used in foundations, walls, and other structural elements.
16. Expert Insights and Opinions
Industry experts emphasize the importance of carefully considering the specific requirements of each application when selecting materials. Factors such as load-bearing capacity, environmental conditions, and cost constraints should be taken into account to ensure optimal performance and safety.
17. Comparative Analysis Tables
Here’s a detailed comparison table highlighting the key properties of Tungsten and Titanium:
Property | Tungsten | Titanium |
---|---|---|
Tensile Strength | 142,000 psi | 63,000 psi |
Density | 19.3 g/cm³ | 4.5 g/cm³ |
Strength-to-Weight | Lower | Higher |
Hardness (Mohs) | 9 | 6 |
Impact Resistance | Low (Brittle) | High |
Corrosion Resistance | Good | Excellent |
Melting Point | 3,410 °C (6,170 °F) | 1,668 °C (3,034 °F) |
Common Applications | Filaments, Welding Rods | Aerospace, Medical Implants |
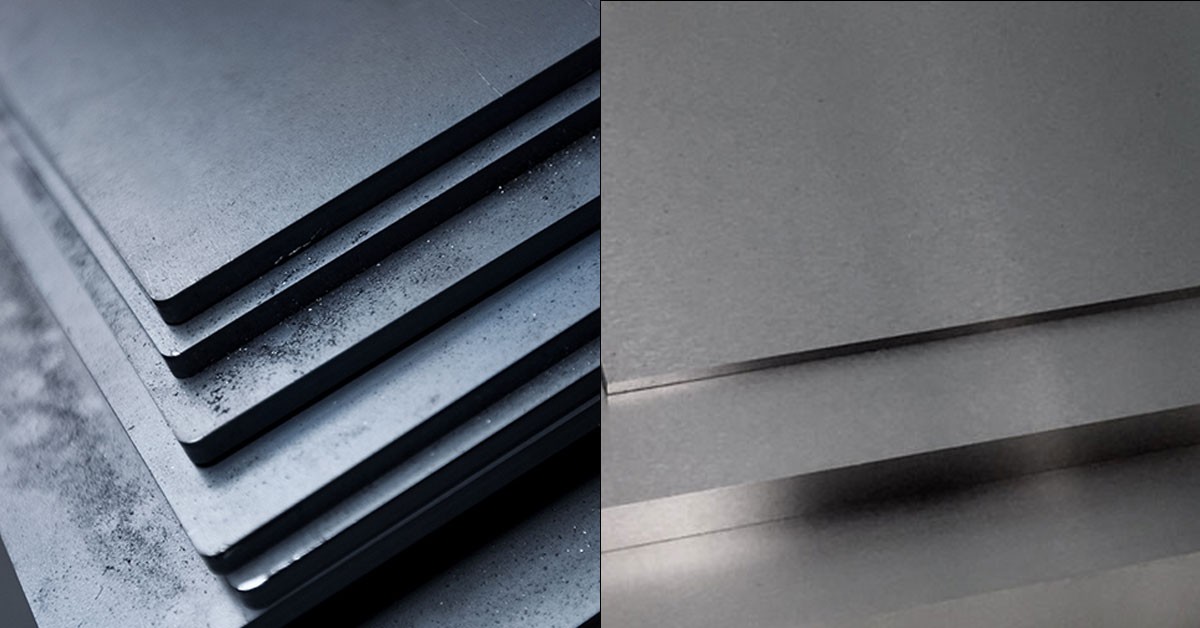
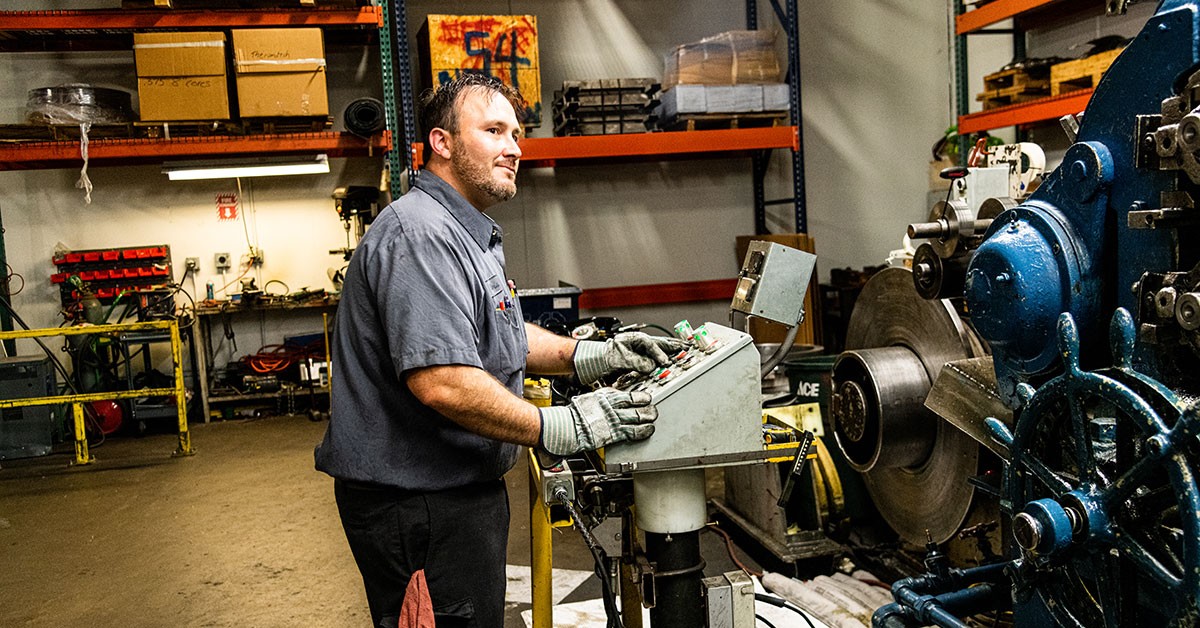
18. Summary: Tungsten vs. Titanium – Which is Stronger?
In summary, while tungsten boasts a higher tensile strength, titanium’s superior strength-to-weight ratio and impact resistance make it a more versatile material for a wider range of applications. The “strongest” metal ultimately depends on the specific requirements of the application.
19. FAQs About Tungsten and Titanium
19.1. What is the primary advantage of using titanium over tungsten?
Titanium has a much better strength-to-weight ratio, making it preferable in applications where weight is a concern.
19.2. Why is tungsten used in light bulb filaments?
Tungsten’s high melting point allows it to withstand the extreme temperatures generated in incandescent light bulbs.
19.3. Which metal is more resistant to corrosion, tungsten or titanium?
Titanium has superior corrosion resistance compared to tungsten.
19.4. Can tungsten be used in aerospace applications?
Yes, tungsten alloys are used in specific high-temperature aerospace applications like rocket nozzles.
19.5. What makes titanium suitable for medical implants?
Titanium is biocompatible, corrosion-resistant, and has a high strength-to-weight ratio, making it ideal for medical implants.
19.6. How does the hardness of tungsten compare to other metals?
Tungsten is one of the hardest metals, with a rating of 9 on the Mohs scale of hardness.
19.7. In what industries is titanium most commonly used?
Titanium is widely used in the aerospace, medical, and sporting goods industries.
19.8. What are the limitations of using tungsten in certain applications?
Tungsten is brittle and prone to shattering upon impact, limiting its use in applications requiring high impact resistance.
19.9. How does alloying affect the strength of tungsten and titanium?
Alloying can significantly enhance the strength, hardness, and other properties of both tungsten and titanium.
19.10. Where can I find more information about metal comparisons?
Visit COMPARE.EDU.VN for detailed and comprehensive metal comparisons.
20. Conclusion: Making Informed Decisions
Choosing the right material requires a comprehensive understanding of its properties and how they align with the specific demands of the application. Tungsten and titanium each offer unique strengths and weaknesses, making them suitable for different purposes. By carefully evaluating these factors, engineers and designers can make informed decisions that ensure optimal performance and longevity. At COMPARE.EDU.VN, we provide the resources and expertise needed to navigate these complex choices and find the best solutions for your needs.
Caption: Our experts are ready to assist you with your metal selection needs. Contact COMPARE.EDU.VN for personalized guidance.
21. Discover More at COMPARE.EDU.VN
Are you still uncertain about which material suits your project best? Visit COMPARE.EDU.VN for an in-depth analysis and comparison of various materials. Our platform offers detailed insights, expert opinions, and comparative data to help you make an informed decision. Whether it’s tensile strength, compressive strength, or any other specific requirement, COMPARE.EDU.VN is your trusted source for comprehensive material comparisons.
Ready to make a decision? Explore COMPARE.EDU.VN today to find the perfect material for your project. Our detailed comparisons and expert advice will guide you toward the best choice, ensuring optimal performance and longevity. Don’t leave your material selection to chance—trust COMPARE.EDU.VN for reliable, comprehensive insights.
For further assistance, contact us at:
Address: 333 Comparison Plaza, Choice City, CA 90210, United States
WhatsApp: +1 (626) 555-9090
Website: compare.edu.vn