How do the temperature changes of two cylinders compare? Understanding temperature dynamics between cylinders is crucial in various scientific and engineering applications. At COMPARE.EDU.VN, we offer in-depth comparisons to help you understand these complex phenomena. By examining the factors influencing temperature variations, we can provide clarity and insights into thermal behavior.
1. Introduction to Cylindrical Temperature Dynamics
Temperature changes in cylinders are governed by principles of heat transfer, involving conduction, convection, and radiation. The interplay of these mechanisms determines how quickly and efficiently heat moves within and between cylinders. Factors such as material properties, dimensions, and ambient conditions all play significant roles in modulating these temperature profiles. Consider two cylinders, each potentially experiencing different environmental conditions or composed of distinct materials. How do their temperature changes compare? The answer is multifaceted, reliant on a range of interactive parameters.
2. Factors Influencing Temperature Changes in Cylinders
Several key factors influence the temperature changes observed in cylinders. These include:
- Material Properties: Thermal conductivity, specific heat capacity, and density all influence how quickly a cylinder heats up or cools down.
- Dimensions: The size and shape of the cylinder, specifically its diameter and length, affect the surface area available for heat transfer.
- Boundary Conditions: The temperature and heat transfer coefficients of the surrounding environment play a crucial role.
- Heat Source: The intensity and type of heat source (e.g., constant heat flux, convective heating) significantly impact temperature distribution.
3. Comparison of Thermal Conductivity
Thermal conductivity (k) is a measure of a material’s ability to conduct heat. Materials with high thermal conductivity, like copper and aluminum, transfer heat more efficiently than materials with low thermal conductivity, such as glass or plastic. If two cylinders of identical dimensions are subjected to the same heat source, the cylinder with the higher thermal conductivity will exhibit more rapid and uniform temperature changes.
Material | Thermal Conductivity (W/m·K) |
---|---|
Copper | 401 |
Aluminum | 237 |
Steel | 50 |
Glass | 1.0 |
Polyethylene | 0.42 |
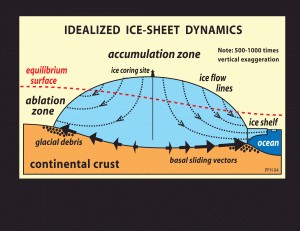
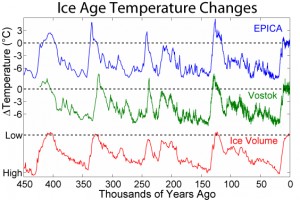
4. Impact of Specific Heat Capacity
Specific heat capacity (c) refers to the amount of heat required to raise the temperature of one kilogram of a substance by one degree Celsius. A material with a high specific heat capacity requires more energy to achieve the same temperature change compared to a material with a low specific heat capacity. Therefore, if two cylinders of the same material but different specific heat capacities are exposed to the same heat source, the cylinder with the lower specific heat capacity will heat up more quickly.
5. Role of Cylinder Dimensions
The dimensions of a cylinder, particularly its radius (r) and length (L), significantly influence its temperature response. A cylinder with a larger surface area will dissipate or absorb heat more readily than one with a smaller surface area.
- Smaller Diameter: Cylinders with smaller diameters generally heat up or cool down more rapidly due to their higher surface area-to-volume ratio.
- Longer Length: Longer cylinders can exhibit more complex temperature gradients along their length, especially if the heat source is localized.
6. Influence of Boundary Conditions
Boundary conditions define the thermal environment surrounding the cylinder. These conditions can include:
- Convection: Heat transfer due to fluid movement (air or liquid) around the cylinder.
- Radiation: Heat transfer through electromagnetic waves.
- Fixed Temperature: Maintaining a constant temperature at the cylinder’s surface.
Different boundary conditions will lead to varying temperature changes. For instance, a cylinder submerged in a well-stirred fluid will experience more uniform temperature changes compared to a cylinder in still air.
7. Types of Heat Sources
The type and intensity of the heat source significantly affect temperature changes in cylinders. Common heat sources include:
- Constant Heat Flux: A constant rate of heat input per unit area.
- Convective Heating: Heat transfer from a hot fluid to the cylinder surface.
- Internal Heat Generation: Heat generated within the cylinder itself (e.g., electrical resistance).
Each heat source creates a unique temperature profile within the cylinder. For example, internal heat generation can lead to a more uniform temperature distribution compared to surface heating.
8. Mathematical Models for Temperature Change
Accurately predicting temperature changes in cylinders often requires the use of mathematical models. These models are typically based on the heat equation, a partial differential equation that describes how temperature varies with time and position.
The general form of the heat equation in cylindrical coordinates is:
$$rho c frac{partial T}{partial t} = k left( frac{1}{r} frac{partial}{partial r} left( r frac{partial T}{partial r} right) + frac{1}{r^2} frac{partial^2 T}{partial theta^2} + frac{partial^2 T}{partial z^2} right) + q$$
Where:
- ( rho ) is the density.
- ( c ) is the specific heat capacity.
- ( T ) is the temperature.
- ( t ) is time.
- ( k ) is the thermal conductivity.
- ( r ), ( theta ), and ( z ) are cylindrical coordinates.
- ( q ) is the heat generation rate per unit volume.
Solving this equation analytically can be complex, especially for non-ideal boundary conditions. Numerical methods, such as finite element analysis (FEA), are often employed to obtain approximate solutions.
9. Finite Element Analysis (FEA) for Thermal Simulation
FEA is a powerful computational technique used to simulate temperature distributions in complex geometries and under various boundary conditions. FEA software divides the cylinder into numerous small elements and solves the heat equation for each element, providing a detailed temperature profile.
Using FEA, engineers and scientists can:
- Predict temperature changes under different operating conditions.
- Optimize cylinder designs for thermal performance.
- Identify potential hotspots and thermal stresses.
10. Case Study: Comparing Two Cylinders
Let’s consider two cylinders:
- Cylinder A: Made of aluminum (k = 237 W/m·K, c = 900 J/kg·K), diameter 5 cm, length 20 cm.
- Cylinder B: Made of steel (k = 50 W/m·K, c = 470 J/kg·K), diameter 5 cm, length 20 cm.
Both cylinders are initially at 20°C and are placed in an environment with a convective heat transfer coefficient of 10 W/m²·K and an ambient temperature of 100°C.
Using FEA, we can simulate the temperature changes over time:
- Cylinder A (Aluminum): Heats up more rapidly due to its higher thermal conductivity. The temperature distribution is more uniform.
- Cylinder B (Steel): Heats up more slowly due to its lower thermal conductivity. The temperature distribution is less uniform.
The simulation results would show that Cylinder A reaches a higher average temperature faster than Cylinder B. This difference highlights the impact of material properties on thermal behavior.
11. Real-World Applications
Understanding temperature changes in cylinders is essential in many engineering applications, including:
- Heat Exchangers: Designing efficient heat exchangers that maximize heat transfer between fluids.
- Engine Cylinders: Managing temperature in internal combustion engines to optimize performance and reduce thermal stress.
- Electronic Cooling: Dissipating heat from electronic components to prevent overheating.
- Nuclear Reactors: Controlling temperature within fuel rods to ensure safe and efficient operation.
12. Advanced Topics in Cylindrical Heat Transfer
Beyond the basics, several advanced topics are relevant to understanding temperature changes in cylinders:
- Transient Heat Transfer: Analyzing temperature changes over time, including heating and cooling rates.
- Non-Uniform Heat Generation: Modeling scenarios where heat is generated unevenly within the cylinder.
- Phase Change Materials (PCMs): Utilizing materials that absorb or release heat during phase transitions (e.g., melting or solidification) to regulate temperature.
- Computational Fluid Dynamics (CFD): Combining fluid flow and heat transfer simulations to analyze complex thermal systems.
13. Transient Heat Transfer Analysis
Transient heat transfer focuses on the time-dependent temperature distribution within a cylinder. This is crucial in applications where cylinders are subjected to varying thermal conditions. The transient heat equation is solved to determine the temperature at any point within the cylinder at any given time.
For a cylinder with constant properties and no internal heat generation, the transient heat equation in cylindrical coordinates can be simplified to:
$$frac{partial T}{partial t} = alpha left( frac{partial^2 T}{partial r^2} + frac{1}{r} frac{partial T}{partial r} right)$$
Where ( alpha = frac{k}{rho c} ) is the thermal diffusivity.
Solving this equation requires specifying initial and boundary conditions, which often leads to complex mathematical solutions. Numerical methods like FEA are commonly used to approximate the temperature distribution over time.
14. Non-Uniform Heat Generation
In some applications, heat generation within a cylinder may not be uniform. For example, in a nuclear fuel rod, the heat generation rate varies with the position within the rod. Modeling non-uniform heat generation requires incorporating a spatially dependent heat source term ( q(r, z) ) into the heat equation:
$$rho c frac{partial T}{partial t} = k left( frac{1}{r} frac{partial}{partial r} left( r frac{partial T}{partial r} right) + frac{partial^2 T}{partial z^2} right) + q(r, z)$$
Solving this equation can be challenging, and numerical methods are typically used to obtain accurate temperature distributions.
15. Phase Change Materials (PCMs)
Phase change materials (PCMs) are substances that absorb or release heat during phase transitions, such as melting or solidification. They can be used to regulate the temperature of cylinders by absorbing excess heat during periods of high thermal load and releasing heat during periods of low thermal load.
The effective heat capacity of a PCM near its phase transition temperature is very high, allowing it to absorb a significant amount of heat with minimal temperature change. PCMs are used in various applications, including thermal energy storage, electronic cooling, and building temperature control.
16. Computational Fluid Dynamics (CFD)
Computational Fluid Dynamics (CFD) is a numerical method used to simulate fluid flow and heat transfer simultaneously. CFD can be used to analyze complex thermal systems involving cylinders, such as heat exchangers or electronic cooling systems.
CFD simulations can provide detailed information about:
- Velocity and pressure distributions in the fluid.
- Temperature distributions in the fluid and solid components.
- Heat transfer coefficients at the cylinder surface.
- Thermal performance of the system under different operating conditions.
By combining CFD with heat transfer analysis, engineers can optimize the design and operation of thermal systems involving cylinders.
17. Comparative Analysis of Cylinders in Heat Exchangers
In heat exchangers, cylinders (often in the form of tubes) are used to transfer heat between two fluids. The efficiency of a heat exchanger depends on several factors, including the thermal conductivity of the tube material, the tube dimensions, and the flow rates and temperatures of the fluids.
Comparing different cylinder materials in heat exchangers involves analyzing their thermal performance under specific operating conditions. For example, copper tubes are often used in heat exchangers due to their high thermal conductivity, but they can be expensive. Aluminum tubes offer a lower-cost alternative, but their lower thermal conductivity may reduce the overall heat exchanger efficiency.
By using mathematical models and numerical simulations, engineers can compare the performance of different cylinder materials and optimize the heat exchanger design for specific applications.
18. Temperature Management in Engine Cylinders
In internal combustion engines, managing the temperature of the cylinder is crucial for optimizing performance and preventing thermal damage. Excessive temperatures can lead to:
- Pre-ignition or knocking.
- Reduced volumetric efficiency.
- Increased thermal stress on engine components.
Engine cylinders are typically cooled using a liquid coolant or air cooling system. The cooling system must be designed to effectively remove heat from the cylinder and maintain a safe operating temperature.
Comparing different cooling strategies involves analyzing their ability to remove heat from the cylinder under various operating conditions. CFD simulations can be used to optimize the design of the cooling system and ensure that the cylinder temperature remains within acceptable limits.
19. Electronic Cooling Applications
In electronic devices, cylinders (often in the form of heat pipes) are used to dissipate heat from electronic components, such as CPUs or GPUs. These components generate a significant amount of heat, which must be removed to prevent overheating and ensure reliable operation.
Heat pipes are hollow cylinders filled with a working fluid that evaporates at the hot end and condenses at the cold end, transferring heat through latent heat of vaporization. The efficiency of a heat pipe depends on several factors, including the working fluid, the cylinder dimensions, and the thermal resistance of the materials.
Comparing different heat pipe designs involves analyzing their ability to transfer heat under specific operating conditions. FEA and CFD simulations can be used to optimize the heat pipe design and ensure that the electronic component temperature remains within acceptable limits.
20. Safety in Nuclear Reactor Fuel Rods
In nuclear reactors, fuel rods are cylindrical components that contain nuclear fuel. The fuel rods generate a significant amount of heat due to nuclear fission. It is crucial to maintain the fuel rod temperature within safe limits to prevent fuel melting or cladding failure.
The fuel rods are typically cooled by a liquid coolant, such as water or liquid metal. The cooling system must be designed to effectively remove heat from the fuel rods and maintain a safe operating temperature.
Comparing different fuel rod designs and cooling strategies involves analyzing their ability to remove heat from the fuel rods under various operating conditions. Mathematical models and numerical simulations are used to ensure that the fuel rod temperature remains within safe limits, even during transient events or accident scenarios.
21. Influence of Surface Finish on Heat Transfer
The surface finish of a cylinder affects its heat transfer characteristics. A rough surface has a larger surface area, which can enhance convective heat transfer. However, it can also increase the emissivity of the surface, leading to higher radiative heat transfer.
Comparing the thermal performance of cylinders with different surface finishes involves analyzing the combined effects of convection and radiation. Experimental measurements and numerical simulations can be used to determine the optimal surface finish for specific applications.
22. Impact of Cylinder Orientation
The orientation of a cylinder in a fluid flow affects its convective heat transfer characteristics. A horizontal cylinder has different heat transfer coefficients compared to a vertical cylinder due to the buoyancy-driven flow patterns.
Comparing the thermal performance of cylinders in different orientations involves analyzing the fluid flow and heat transfer patterns around the cylinder. CFD simulations can be used to determine the optimal orientation for specific applications.
23. Importance of Accurate Material Properties
Accurate material properties, such as thermal conductivity, specific heat capacity, and density, are crucial for accurate heat transfer analysis. These properties can vary with temperature, so it is important to use temperature-dependent properties in simulations.
Comparing the thermal performance of cylinders using different material property data involves analyzing the sensitivity of the results to the material properties. Experimental measurements and literature data can be used to obtain accurate material properties for specific applications.
24. Optimization Techniques for Thermal Design
Optimization techniques can be used to design cylinders with optimal thermal performance. These techniques involve varying design parameters, such as cylinder dimensions, material properties, and cooling strategies, to minimize temperature or maximize heat transfer.
Comparing different optimization techniques involves analyzing their ability to find the global optimum and their computational efficiency. Gradient-based optimization methods and genetic algorithms are commonly used for thermal design optimization.
25. Advanced Cooling Strategies
Advanced cooling strategies can be used to enhance the thermal performance of cylinders. These strategies include:
- Microchannel Cooling: Using small channels to increase the surface area for heat transfer.
- Spray Cooling: Spraying a liquid onto the cylinder surface to enhance evaporative cooling.
- Thermoelectric Cooling: Using thermoelectric devices to actively remove heat from the cylinder.
Comparing the performance of different cooling strategies involves analyzing their ability to remove heat from the cylinder and their energy consumption. Experimental measurements and numerical simulations can be used to evaluate the effectiveness of advanced cooling strategies.
26. Industrial Applications of Cylindrical Thermal Analysis
Many industries rely on accurate analysis of cylindrical thermal dynamics. These include:
- Aerospace: Managing heat in aircraft engines and electronic systems.
- Automotive: Cooling engines and optimizing heat exchangers.
- Electronics: Dissipating heat from semiconductors.
- Manufacturing: Controlling temperature in industrial processes.
- Energy: Optimizing heat transfer in power plants.
27. The Future of Cylindrical Thermal Management
The field of cylindrical thermal management continues to evolve. Future trends include:
- Development of new high-performance materials.
- Improved simulation techniques for complex geometries.
- Integration of artificial intelligence for thermal optimization.
- Increased focus on energy efficiency and sustainability.
28. Key Takeaways
- Temperature changes in cylinders are influenced by several factors, including material properties, dimensions, boundary conditions, and heat source.
- Mathematical models and numerical simulations, such as FEA and CFD, are essential for accurately predicting temperature distributions.
- Understanding temperature dynamics is critical in various engineering applications, including heat exchangers, engine cylinders, electronic cooling, and nuclear reactors.
29. Frequently Asked Questions (FAQ)
-
What is thermal conductivity?
Thermal conductivity is a measure of a material’s ability to conduct heat. -
How does specific heat capacity affect temperature change?
Specific heat capacity determines how much energy is needed to change the temperature of a substance. -
What are boundary conditions in heat transfer?
Boundary conditions define the thermal environment surrounding an object, such as temperature and heat transfer coefficients. -
What is FEA used for in thermal analysis?
FEA is used to simulate temperature distributions in complex geometries. -
How do heat pipes work?
Heat pipes transfer heat through the evaporation and condensation of a working fluid. -
Why is temperature management important in engine cylinders?
To optimize performance and prevent thermal damage. -
What are PCMs?
Phase Change Materials are used to regulate temperature by absorbing or releasing heat during phase transitions. -
How does surface finish affect heat transfer?
Surface finish affects convective and radiative heat transfer. -
What is CFD?
Computational Fluid Dynamics is used to simulate fluid flow and heat transfer. -
Why is accurate material property data crucial?
Accurate material properties are essential for precise heat transfer analysis.
30. Need More Help?
Navigating the complexities of temperature change and thermal dynamics can be daunting. At COMPARE.EDU.VN, we strive to provide comprehensive and clear comparisons to aid your understanding and decision-making. Whether you’re comparing different materials, designs, or strategies, our resources are designed to offer objective insights.
31. Let COMPARE.EDU.VN Assist You
Ready to dive deeper? Visit COMPARE.EDU.VN to explore detailed comparisons and make informed decisions today. Our platform offers a wide range of analyses tailored to meet your specific needs.
To gain a competitive edge and make informed decisions, visit COMPARE.EDU.VN today.
Address: 333 Comparison Plaza, Choice City, CA 90210, United States
Whatsapp: +1 (626) 555-9090
Website: compare.edu.vn