Comparing motors can be a daunting task, but COMPARE.EDU.VN simplifies the process. This in-depth analysis explores the critical differences between NEMA and IEC motor standards, guiding you to the optimal choice for your specific application. We delve into electrical and mechanical variations, providing a comprehensive comparison of motor specifications and standards.
1. Key Electrical Differences in Motor Standards
Understanding the electrical nuances between NEMA and IEC standards is crucial for selecting the right motor. These differences impact performance, compatibility, and overall efficiency.
1.1 Power Output: HP vs. kW
Motor power is the capability to move a load at a specific speed. NEMA standards quantify this using Horsepower (HP), while IEC standards use Kilowatts (kW). Understanding the conversion is essential for comparing motors across standards.
From | Multiply By | To |
---|---|---|
HP | 0.736 | kW |
kW | 1.341 | HP |
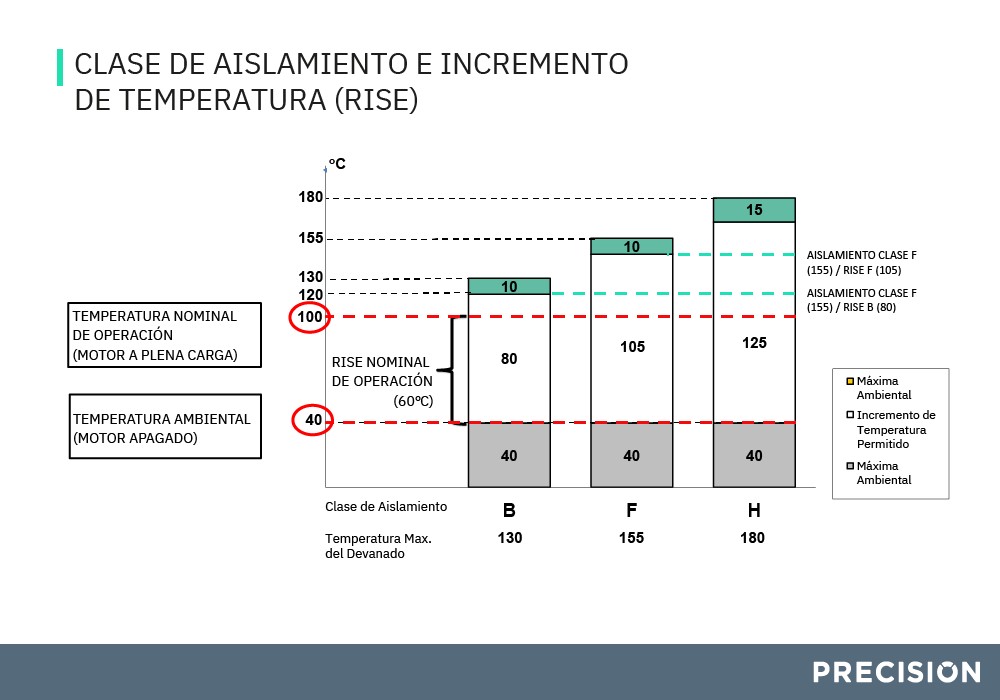
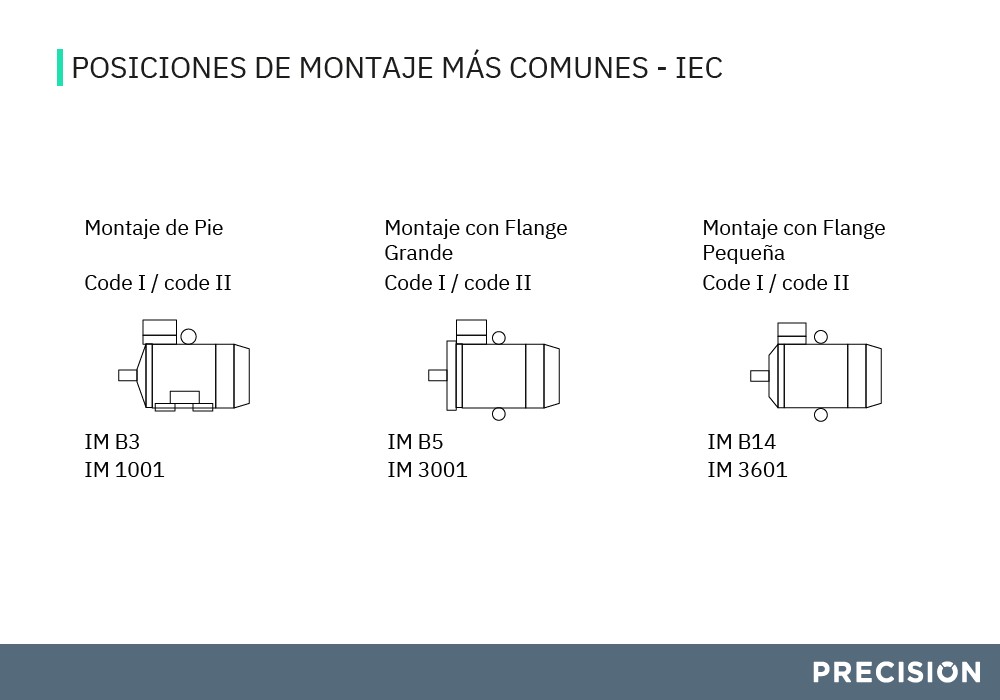
1.2 Voltage, Frequency, and Speed Considerations
NEMA motors typically operate at 230V and 460V, while IEC motors commonly use 380V and 400V. These variations reflect different regional power supply standards. Motor speed, measured in Revolutions Per Minute (RPM), also varies based on frequency (Hz).
Motor | Synchronous Speed |
---|---|
50 Hz | |
2 Pole | 3,000 RPM |
4 Pole | 1,500 RPM |
6 Pole | 1,000 RPM |
8 Pole | 750 RPM |
While NEMA is often associated with 60 Hz and IEC with 50 Hz, motors compliant with both standards and frequencies are available.
1.3 Service Factor (SF) Explained
The Service Factor (SF) indicates the motor’s ability to handle continuous overload under specific conditions. It’s distinct from momentary overload capacity. IEC motors commonly have SFs of 1.00 or 1.15, while NEMA motors can have SFs up to 1.25 at 60Hz, allowing for higher continuous overload capacity.
1.4 Insulation Class and Temperature Rise Implications
Insulation class defines the maximum internal temperature a motor’s winding can withstand. Common classes include A, B, F, and H, with Class F (155°C) being the most prevalent. Temperature Rise (RISE) is the difference between ambient temperature when the motor is off and the operating temperature at full power.
1.5 Efficiency Standards: NEMA vs. IEC
Electrical efficiency measures how effectively a motor converts electrical power into useful mechanical work. Both NEMA and IEC have standard testing methods, but the classification differs. NEMA categorizes motors into standard, high, and premium efficiency, each with minimum efficiency requirements. IEC defines efficiency classes as IE1, IE2, IE3, IE4, and IE5 (for some types), with each class representing a higher efficiency level.
IEC | NEMA |
---|---|
IE1 | Below Standard Efficiency |
IE2 | High Efficiency |
IE3 | Premium Efficiency |
IE4 | Not Standardized |
IE5 | Not Standardized |
Choosing high-efficiency motors reduces energy consumption and operational costs, contributing to lower carbon emissions.
2. Mechanical Differences: NEMA and IEC Motor Standards
Understanding the mechanical differences between NEMA and IEC motors helps ensure proper fit, function, and integration within your applications. These differences affect mounting, cooling, and overall motor durability.
2.1 Enclosure and Cooling Methods
NEMA motors use letter codes to indicate enclosure type (open or closed) and ventilation method (e.g., FC – Fan Cooled, BC – Blower Cooled). IEC motors use the IC (International Cooling) code. Modern NEMA motors also include the equivalent IC code for easier comparison. The IP (Ingress Protection) rating, present in both standards, indicates protection against dust and water.
2.2 Mounting Positions Explained
NEMA and IEC use different codes for motor mounting positions. NEMA’s standard is F1 (horizontal floor mount, junction box on the left). IEC’s standard is IMB3 (junction box on top). IEC codes also specify flange positions (IM B14, IM B35).
2.3 Terminal Box Differences
The standard terminal box position for NEMA is on the left (F1), while for IEC, it’s on top (B3). Both standards allow for customization. Another difference is that NEMA motors have loose wires in the box, whereas IEC motors have terminal blocks.
2.4 Frame Sizes and Dimensions
Frame codes indicate standard motor dimensions. Motors with the same frame code have the same dimensions regardless of manufacturer. NEMA uses inches (first two digits are 4 times the shaft center height in inches), while IEC uses millimeters for shaft center height. This difference in units means NEMA and IEC frames aren’t exactly equivalent. NEMA and IEC also use different lettering for dimensions (e.g., shaft diameter is “U” in NEMA and “D” in IEC). IEC has a wider range of frame sizes (56mm to 1000mm), and NEMA lacks equivalents for every IEC frame.
2.5 Torque Characteristics in Motor Standards
Both NEMA and IEC motors have speed-torque curves. However, they use different terminology for parameters. For example, NEMA uses “locked-rotor torque,” while IEC uses “starting torque.”
3. NEMA or IEC: Making the Right Choice
Choosing between NEMA and IEC motors requires careful consideration of electrical and mechanical differences. COMPARE.EDU.VN is here to assist you.
3.1 Standards and Regulations
- NEMA: Predominantly used in North America, NEMA offers flexibility in design tolerances and customization.
- IEC: Globally accepted, IEC promotes uniformity, interoperability, and easier substitution.
3.2 Size and Configuration
- NEMA: Offers a wider range of sizes and configurations, including options for severe duty and special environments.
- IEC: Standardized sizes and mounting, leading to less variability and often more compact designs.
3.3 Efficiency and Service Factor
- NEMA: Offers standard, high, and premium efficiency levels and higher service factors for continuous overload.
- IEC: Classifies efficiency (IE1-IE5) but typically has a standardized service factor, potentially limiting overload capacity.
3.4 Voltage and Frequency
- NEMA/IEC: While NEMA is associated with North American voltages/frequencies (60Hz, 230V/460V) and IEC with international standards (50Hz, 380V/400V), both types can adapt for global use.
3.5 Cost and Availability
- NEMA: May have higher costs and limited availability outside North America due to specific customizations.
- IEC: Generally more accessible and available globally, simplifying acquisition and replacement.
The choice often depends on specific application needs, operating environment, performance requirements, and long-term costs. NEMA motors are suitable for North American applications needing particular specifications or overload capabilities. IEC motors are ideal for projects prioritizing standardization and global availability.
Consider this information to make informed decisions aligning with your project or plant objectives.
Need expert advice on NEMA or IEC motors for your operations? Contact us at 333 Comparison Plaza, Choice City, CA 90210, United States, Whatsapp: +1 (626) 555-9090, or visit COMPARE.EDU.VN.
4. Understanding Motor Applications and Selection
Selecting the right motor requires a deep understanding of specific applications. This section provides insights into various scenarios and considerations for both NEMA and IEC standards.
4.1 Industrial Automation
In industrial automation, motors are crucial for driving conveyors, pumps, and robotic systems. Key factors include reliability, efficiency, and precise control. IEC motors are often preferred due to their standardization and compact design, which simplifies integration into automated systems. However, NEMA motors may be chosen for heavy-duty applications requiring higher overload capacity.
4.2 HVAC Systems
Heating, Ventilation, and Air Conditioning (HVAC) systems rely on motors for fans, blowers, and compressors. Efficiency and quiet operation are paramount. Both NEMA and IEC offer high-efficiency motors suitable for HVAC applications. IEC motors may be favored in international markets, while NEMA motors are common in North American HVAC systems.
4.3 Water and Wastewater Treatment
Motors in water and wastewater treatment plants drive pumps and mixers. These applications demand robust motors capable of withstanding harsh environments. NEMA motors are often selected for their rugged construction and ability to handle demanding conditions. IEC motors with appropriate ingress protection (IP ratings) are also viable options.
4.4 Renewable Energy Systems
Wind turbines and solar tracking systems utilize motors for various functions. Reliability and efficiency are critical in these applications. IEC motors are commonly used in wind turbines due to their global acceptance and standardized designs. Solar tracking systems may employ either NEMA or IEC motors, depending on the specific requirements of the system.
4.5 Electric Vehicles (EVs)
Electric Vehicles (EVs) need high-performance, compact, and efficient motors. These applications are pushing motor technology boundaries. While many EVs use custom-designed motors, both NEMA and IEC standards inform design principles. Efficiency, power density, and thermal management are critical considerations.
5. Optimizing Motor Performance: Essential Tips
To ensure optimal motor performance and longevity, consider these essential tips, regardless of whether you choose NEMA or IEC standards.
5.1 Proper Installation and Alignment
Correct installation is crucial. Ensure proper alignment to prevent premature wear and vibration. Misalignment can lead to bearing failure, shaft damage, and reduced motor lifespan.
5.2 Regular Maintenance and Inspection
Implement a routine maintenance schedule. Inspect motors regularly for signs of wear, overheating, or unusual noise. Check bearings, windings, and connections.
5.3 Effective Lubrication
Proper lubrication is essential for bearing health. Follow the manufacturer’s recommendations for lubricant type and frequency of application. Avoid over-lubrication, which can damage bearings.
5.4 Thermal Management
Monitor motor temperature. Overheating can degrade insulation and reduce motor life. Ensure adequate ventilation and cooling. Consider using thermal overload protection.
5.5 Vibration Analysis
Use vibration analysis to detect potential problems early. Changes in vibration patterns can indicate bearing wear, misalignment, or other issues.
5.6 Motor Protection Devices
Install appropriate motor protection devices. Overload relays, circuit breakers, and surge protectors can prevent damage from overloads, short circuits, and voltage spikes.
5.7 Variable Frequency Drives (VFDs)
Consider using Variable Frequency Drives (VFDs). VFDs allow for precise speed control and can improve energy efficiency. Ensure compatibility between the motor and VFD.
5.8 Energy Efficiency Upgrades
Upgrade to high-efficiency motors. Replacing older, less efficient motors with newer models can significantly reduce energy consumption and operating costs.
5.9 Data Logging and Monitoring
Implement data logging and monitoring systems. Tracking motor performance data can help identify trends and potential problems.
5.10 Professional Expertise
Consult with motor experts. Seek professional advice for complex applications or troubleshooting. Regular consultations can help optimize motor performance and prevent costly downtime.
6. Navigating the Future of Motor Technology
The landscape of motor technology is continuously evolving. Emerging trends are shaping the future of both NEMA and IEC motors, driving innovation and efficiency.
6.1 Increased Efficiency Standards
Regulatory bodies are pushing for higher efficiency standards. Expect stricter regulations for both NEMA and IEC motors, encouraging manufacturers to develop more efficient designs.
6.2 Smart Motors and IoT Integration
Smart motors with integrated sensors and connectivity are becoming more prevalent. These motors provide real-time data on performance, enabling predictive maintenance and optimization.
6.3 Advanced Materials and Manufacturing
New materials and manufacturing techniques are improving motor performance. Innovations in magnet technology, winding materials, and cooling systems are enhancing efficiency and power density.
6.4 Electrification and Sustainability
The global push for electrification is driving motor innovation. Electric vehicles, renewable energy systems, and industrial automation are creating demand for high-performance, sustainable motors.
6.5 Customization and Flexibility
Manufacturers are offering more customizable motor solutions. Tailoring motors to specific applications can improve performance and efficiency.
6.6 Digital Twins and Simulation
Digital twins and simulation tools are used to design and optimize motors. These technologies enable engineers to predict performance, identify potential problems, and refine designs.
6.7 Predictive Maintenance and AI
Artificial intelligence (AI) is transforming motor maintenance. AI-powered predictive maintenance systems analyze data from sensors to predict failures and optimize maintenance schedules.
6.8 Standardization and Interoperability
Efforts to improve standardization and interoperability are ongoing. Streamlining motor standards and interfaces can reduce complexity and cost.
6.9 Skills and Training
The evolving motor landscape requires skilled professionals. Investing in training and education is essential to ensure that technicians and engineers can effectively install, maintain, and optimize modern motors.
6.10 Collaboration and Partnerships
Collaboration between manufacturers, researchers, and end-users is driving innovation. Partnerships can accelerate the development and adoption of new motor technologies.
7. FAQs: NEMA vs. IEC Motor Standards
To further assist you in making informed decisions, we’ve compiled a list of frequently asked questions regarding NEMA and IEC motor standards.
7.1 What is the primary difference between NEMA and IEC motor standards?
NEMA (National Electrical Manufacturers Association) is primarily used in North America, while IEC (International Electrotechnical Commission) is used globally. They differ in design tolerances, measurement units, and testing methods.
7.2 Which standard is better, NEMA or IEC?
Neither standard is inherently “better.” The choice depends on your application, location, and specific requirements. NEMA offers more customization, while IEC provides better standardization.
7.3 Can NEMA and IEC motors be used interchangeably?
Not directly. They have different dimensions, voltages, and performance characteristics. However, motors can be designed to meet both standards for global use.
7.4 What are the different efficiency classes in IEC motors?
IEC defines efficiency classes as IE1 (standard), IE2 (high), IE3 (premium), IE4 (super premium), and IE5 (ultra premium). Each class represents a higher level of efficiency.
7.5 What is the service factor (SF) in a motor?
The service factor indicates the motor’s ability to handle continuous overload. NEMA motors often have higher SFs than IEC motors.
7.6 How do I convert between horsepower (HP) and kilowatts (kW)?
1 HP = 0.746 kW, and 1 kW = 1.34 HP.
7.7 What is the IP rating on a motor?
The IP (Ingress Protection) rating indicates the motor’s protection against dust and water. Higher numbers indicate better protection.
7.8 How important is motor efficiency?
Motor efficiency is crucial for reducing energy consumption and operating costs. High-efficiency motors also contribute to environmental sustainability.
7.9 What are the common voltage levels for NEMA and IEC motors?
NEMA motors typically operate at 230V and 460V, while IEC motors commonly use 380V and 400V.
7.10 Where can I find more information on NEMA and IEC motor standards?
Visit the NEMA and IEC websites for detailed information on their respective standards. COMPARE.EDU.VN also offers valuable comparisons and resources.
COMPARE.EDU.VN is dedicated to providing comprehensive comparisons and expert insights to help you make informed decisions. Contact us at 333 Comparison Plaza, Choice City, CA 90210, United States, Whatsapp: +1 (626) 555-9090, or visit compare.edu.vn for more information.
By understanding the nuances of both NEMA and IEC motor standards, you can select the ideal motor for your specific requirements, ensuring optimal performance, efficiency, and longevity.