Comparing metal hardness with mineral hardness is possible using standardized scales; however, it’s crucial to understand their differences. Metal hardness, often measured using tests like Rockwell, Vickers, or Brinell, reflects a metal’s resistance to indentation. Mineral hardness, assessed with the Mohs scale, indicates a mineral’s resistance to scratching. While both scales quantify resistance to deformation, they use different methods and are not directly interchangeable. For comprehensive materials comparison, visit COMPARE.EDU.VN.
1. Understanding Hardness: Metal vs. Mineral
Hardness, in materials science, fundamentally refers to a material’s resistance to localized plastic deformation caused by indentation or scratching. However, the context and measurement of hardness differ significantly between metals and minerals. It’s crucial to understand these differences before attempting any comparison. Let’s explore the nuances of each:
1.1. What is Metal Hardness?
Metal hardness refers to a metal’s ability to resist permanent deformation when a force is applied, such as indentation or scratching. It is a critical property determining a metal’s suitability for various applications, ranging from structural components to cutting tools.
Several methods are used to measure metal hardness, each with its own scale and application:
- Rockwell Hardness Test: This test measures the depth of indentation of an indenter (usually a steel ball or diamond cone) under a specific load. The Rockwell scale is widely used due to its speed and ease of use.
- Vickers Hardness Test: The Vickers test uses a diamond indenter in the shape of a square-based pyramid. It measures the indentation’s area, providing a precise hardness value suitable for various materials and hardness ranges.
- Brinell Hardness Test: This test uses a hardened steel or carbide ball to create an indentation. The Brinell hardness number (BHN) is determined by dividing the applied load by the surface area of the indentation. It is commonly used for testing large, non-homogeneous materials.
These tests provide quantitative measures of a metal’s resistance to indentation.
1.2. What is Mineral Hardness?
Mineral hardness refers to a mineral’s resistance to scratching, rather than indentation. The most commonly used scale for measuring mineral hardness is the Mohs scale, a qualitative ordinal scale developed by German mineralogist Friedrich Mohs in 1812.
The Mohs scale ranks ten minerals from 1 (talc, the softest) to 10 (diamond, the hardest). A mineral’s hardness is determined by its ability to scratch a softer mineral and be scratched by a harder one.
Mohs Hardness Scale
Hardness | Mineral | Common Test |
---|---|---|
1 | Talc | Can be scratched by a fingernail |
2 | Gypsum | Can be scratched by a fingernail |
3 | Calcite | Can be scratched by a copper penny |
4 | Fluorite | Can be easily scratched by a knife |
5 | Apatite | Can be scratched by a knife with difficulty |
6 | Orthoclase | Can scratch glass and be scratched by a file |
7 | Quartz | Can scratch glass easily |
8 | Topaz | Scratches quartz |
9 | Corundum | Scratches topaz |
10 | Diamond | Can only be scratched by another diamond |
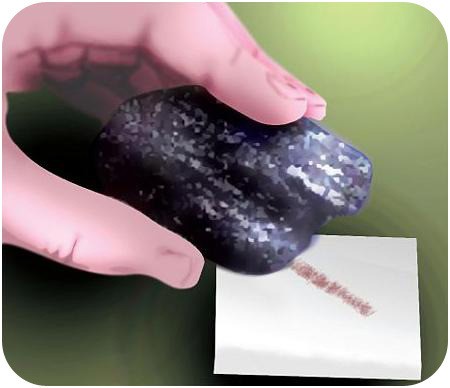
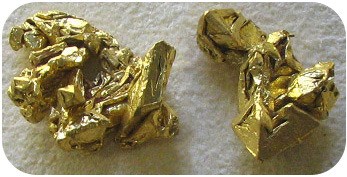
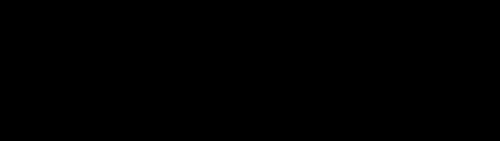
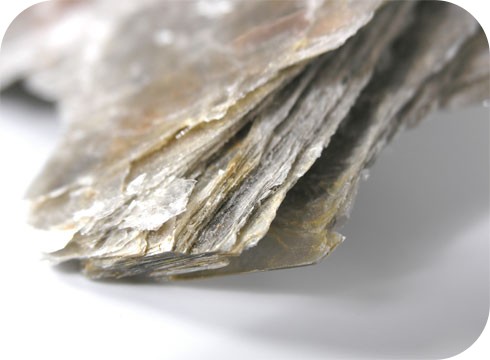
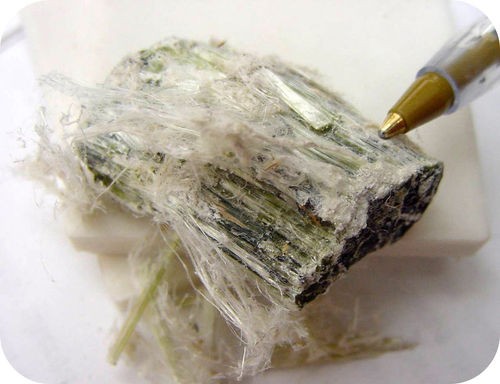
The Mohs scale is useful for field identification of minerals due to its simplicity. However, it is not linear; the difference in absolute hardness between corundum (9) and diamond (10) is much greater than the difference between talc (1) and gypsum (2).
1.3. Why Direct Comparison is Difficult
Directly comparing metal hardness with mineral hardness is challenging due to the fundamental differences in how these properties are measured and defined.
- Measurement Method: Metal hardness tests measure resistance to indentation, while mineral hardness (Mohs scale) measures resistance to scratching. These are different types of mechanical stress.
- Scale Type: Metal hardness tests provide quantitative, interval, or ratio scale measurements. The Mohs scale is a qualitative, ordinal scale. The intervals between hardness values are not uniform or proportional to actual hardness differences.
- Material Properties: Metals and minerals have distinct material properties. Metals are generally ductile and malleable, while minerals can be brittle and anisotropic (having properties that vary with direction).
Therefore, converting hardness values from one scale to another is not straightforward and often requires empirical correlations or conversion tables that are specific to certain materials.
The streak of hematite across an unglazed porcelain plate is red-brown.
2. Methods for Assessing Metal Hardness
2.1. Rockwell Hardness Test
The Rockwell Hardness Test is one of the most widely used methods for determining the hardness of metals. It’s appreciated for its speed, ease of use, and minimal sample preparation requirements.
2.1.1. Principles of the Rockwell Test
The Rockwell test measures the depth of penetration of an indenter under a large load compared to the penetration made by a preload. The indenter can be either a diamond cone (for harder materials) or a steel ball (for softer materials).
The test involves the following steps:
- A minor load (preload) is applied to the sample using the indenter. This establishes a baseline depth.
- A major load is applied, increasing the depth of penetration.
- The major load is removed, and the elastic recovery is measured.
- The Rockwell hardness number is calculated based on the difference in penetration depth between the minor and major loads.
2.1.2. Rockwell Scales
Different Rockwell scales are used depending on the material’s hardness and the indenter type. Each scale is identified by a letter. Here are some common Rockwell scales:
Scale | Indenter | Major Load (kgf) | Typical Materials |
---|---|---|---|
Rockwell A | Diamond Cone | 60 | Cemented carbides, thin steel, shallow case-hardened steel |
Rockwell B | 1/16″ Steel Ball | 100 | Copper alloys, soft steels, aluminum alloys |
Rockwell C | Diamond Cone | 150 | Hardened steel, hard cast irons, pearlitic malleable iron, titanium |
Rockwell D | Diamond Cone | 100 | Shallow case-hardened steel, medium-hard steels |
Rockwell E | 1/8″ Steel Ball | 100 | Aluminum, magnesium, and other soft metals |
Rockwell F | 1/16″ Steel Ball | 60 | Annealed copper alloys, thin soft sheet metals |
Rockwell G | 1/16″ Steel Ball | 150 | Phosphor bronze, beryllium copper, malleable irons |
2.1.3. Advantages and Limitations
-
Advantages:
- Speed and Simplicity: The Rockwell test is quick and easy to perform, making it suitable for production environments.
- Minimal Sample Preparation: Requires minimal surface preparation compared to other hardness tests.
- Direct Reading: The hardness value is read directly from the machine, eliminating the need for manual measurement.
- Versatility: A wide range of scales allows testing various materials with different hardness levels.
-
Limitations:
- Limited Accuracy: Less precise than other methods like Vickers, especially for very hard or very soft materials.
- Scale Dependence: Results are scale-dependent; it’s essential to choose the appropriate scale for the material being tested.
- Not Suitable for Small Areas: The indentation size can be relatively large, making it unsuitable for testing small or thin samples.
2.2. Vickers Hardness Test
The Vickers Hardness Test is another widely used method for measuring the hardness of materials. It is particularly useful for testing small areas or thin samples and provides a more precise measurement compared to the Rockwell test.
2.2.1. Principles of the Vickers Test
The Vickers test uses a diamond indenter in the shape of a square-based pyramid with an angle of 136 degrees between opposite faces. The indenter is pressed into the material under a specific load, and the area of the resulting indentation is measured using an optical microscope.
The Vickers hardness number (HV) is calculated using the formula:
$$HV = frac{1.854 cdot F}{d^2}$$
Where:
- (F) is the applied load in kilograms-force (kgf)
- (d) is the arithmetic mean of the two diagonals of the indentation in millimeters (mm)
2.2.2. Procedure of the Vickers Test
- The sample surface is prepared to be smooth and clean.
- The sample is placed on the testing machine, and the Vickers indenter is brought into contact with the surface.
- A load is applied for a specific dwell time (usually 10-15 seconds).
- The load is removed, and the indentation is measured using an optical microscope.
- The lengths of the two diagonals of the indentation are measured, and their arithmetic mean is calculated.
- The Vickers hardness number (HV) is calculated using the formula mentioned above.
2.2.3. Advantages and Limitations
-
Advantages:
- High Accuracy: The Vickers test is more accurate than the Rockwell test, especially for hard materials.
- Versatility: Suitable for testing a wide range of materials, from soft metals to hard ceramics.
- Small Indentation Size: The indentation size is relatively small, making it suitable for testing small areas or thin samples.
- Single Scale: A single Vickers scale can be used for all materials by varying the applied load.
-
Limitations:
- Time-Consuming: The Vickers test is slower than the Rockwell test due to the need for optical measurement of the indentation.
- Surface Preparation: Requires more surface preparation compared to the Rockwell test.
- Subjectivity: The accuracy of the measurement depends on the operator’s skill in measuring the indentation diagonals.
2.3. Brinell Hardness Test
The Brinell Hardness Test is another method used to measure the hardness of materials, particularly large and non-homogeneous samples.
2.3.1. Principles of the Brinell Test
The Brinell test uses a hardened steel or carbide ball to create an indentation in the material being tested. The Brinell hardness number (BHN) is determined by dividing the applied load by the surface area of the indentation.
The Brinell hardness number (BHN) is calculated using the formula:
$$BHN = frac{2F}{pi D (D – sqrt{D^2 – d^2})}$$
Where:
- (F) is the applied load in kilograms-force (kgf)
- (D) is the diameter of the indenter ball in millimeters (mm)
- (d) is the diameter of the indentation in millimeters (mm)
2.3.2. Procedure of the Brinell Test
- The sample surface is prepared to be smooth and clean.
- The sample is placed on the testing machine, and the Brinell ball is brought into contact with the surface.
- A load is applied for a specific dwell time (usually 10-15 seconds).
- The load is removed, and the diameter of the indentation is measured using an optical microscope.
- The Brinell hardness number (BHN) is calculated using the formula mentioned above.
2.3.3. Advantages and Limitations
-
Advantages:
- Suitable for Non-Homogeneous Materials: The large indentation size averages out local variations in hardness, making it suitable for testing non-homogeneous materials like castings and forgings.
- Ease of Use: The Brinell test is relatively simple to perform.
-
Limitations:
- Low Accuracy for Hard Materials: The Brinell test is less accurate for very hard materials because the ball indenter can deform.
- Large Indentation Size: The large indentation size can damage the sample and may not be suitable for small or thin samples.
- Surface Preparation: Requires more surface preparation compared to the Rockwell test.
This mineral is shiny, very soft, heavy, and gold in color, and is actually gold.
3. Understanding Mineral Hardness: The Mohs Scale
3.1. The Origin and Purpose of the Mohs Scale
The Mohs scale of mineral hardness, created in 1812 by German mineralogist Friedrich Mohs, is a qualitative ordinal scale that characterizes the scratch resistance of various minerals through the ability of a harder material to scratch a softer material. This scale is one of the oldest and simplest methods for identifying minerals, especially in the field where sophisticated testing equipment is not available.
3.2. Minerals of the Mohs Scale and Their Characteristics
The Mohs scale consists of ten minerals, each assigned a hardness value from 1 to 10. These minerals serve as reference points for determining the relative hardness of other materials. The minerals are listed in order of increasing hardness:
- Talc (Hardness 1): Talc is one of the softest minerals and can be easily scratched by a fingernail. It has a greasy feel and is often used in talcum powder.
- Gypsum (Hardness 2): Gypsum is slightly harder than talc but can still be scratched by a fingernail. It is commonly found in drywall and plaster.
- Calcite (Hardness 3): Calcite can be scratched by a copper penny. It is a primary component of limestone and marble.
- Fluorite (Hardness 4): Fluorite can be easily scratched by a steel knife. It is used in the production of hydrofluoric acid and as a flux in metallurgy.
- Apatite (Hardness 5): Apatite can be scratched by a steel knife with difficulty. It is a phosphate mineral found in teeth and bones.
- Orthoclase (Feldspar) (Hardness 6): Orthoclase can scratch glass but can be scratched by a steel file. It is a common rock-forming mineral.
- Quartz (Hardness 7): Quartz can easily scratch glass. It is one of the most abundant minerals on Earth and is used in various applications, including glassmaking and electronics.
- Topaz (Hardness 8): Topaz scratches quartz. It is a silicate mineral often used as a gemstone.
- Corundum (Hardness 9): Corundum scratches topaz. It includes minerals like ruby and sapphire, which are known for their hardness and use in abrasives.
- Diamond (Hardness 10): Diamond is the hardest known mineral and can only be scratched by another diamond. It is used in cutting tools and as a gemstone.
3.3. How to Use the Mohs Scale for Mineral Identification
Using the Mohs scale for mineral identification involves a simple scratch test:
-
Obtain a Sample: Acquire a sample of the unknown mineral you want to identify.
-
Gather Tools: Collect the reference minerals from the Mohs scale or common objects with known hardness values, such as a fingernail (approximately 2.5), a copper penny (approximately 3.5), a steel knife (approximately 5.5), and a glass plate (approximately 5.5).
-
Perform Scratch Tests:
- Try to scratch the unknown mineral with each reference mineral or object.
- Start with the softest reference mineral (talc) and work your way up the scale.
- Observe whether the reference mineral leaves a scratch on the unknown mineral or vice versa.
-
Determine Hardness: The hardness of the unknown mineral is determined by the hardest reference mineral that it can scratch and the softest reference mineral that can scratch it. For example, if the unknown mineral can scratch apatite (5) but is scratched by orthoclase (6), its hardness is between 5 and 6.
-
Identify the Mineral: Compare the determined hardness to mineral identification tables to identify the mineral. Keep in mind that other properties, such as color, luster, cleavage, and fracture, should also be considered for accurate identification.
3.4. Limitations of the Mohs Scale
Despite its simplicity and usefulness, the Mohs scale has several limitations:
- Qualitative and Ordinal: The Mohs scale is a qualitative scale that provides a relative measure of hardness. The intervals between the hardness values are not uniform or proportional to the actual hardness differences. For example, the difference in absolute hardness between corundum (9) and diamond (10) is much greater than the difference between talc (1) and gypsum (2).
- Not Suitable for All Materials: The Mohs scale is primarily designed for minerals and is not suitable for measuring the hardness of metals, ceramics, or other synthetic materials.
- Subjectivity: The scratch test can be subjective, and the results may vary depending on the observer’s skill and experience.
- Limited Range: The scale only ranges from 1 to 10, which may not be sufficient for distinguishing between materials with very high or very low hardness values.
(a) Diamond has an adamantine luster. (b) Quartz is not sparkly and has a vitreous, or glassy, luster. (b) Sulfur reflects less light than quartz, so it has a resinous luster.
4. Bridging the Gap: Conversion and Correlation Attempts
While direct comparison between metal and mineral hardness scales is problematic, there have been attempts to correlate these scales through empirical relationships and conversion charts. These correlations are often specific to certain materials and conditions and should be used with caution.
4.1. Empirical Correlations
Empirical correlations involve establishing a mathematical relationship between different hardness scales based on experimental data. These correlations are typically derived by measuring the hardness of a set of materials using both metal hardness tests (e.g., Rockwell, Vickers, Brinell) and the Mohs scale.
The resulting data are then used to develop a regression equation that relates the Mohs hardness to the metal hardness values. For example, one such correlation might take the form:
$$Mohs Hardness = a cdot Vickers Hardness + b$$
Where (a) and (b) are constants determined from the experimental data.
However, empirical correlations have several limitations:
- Material Dependence: The correlation is only valid for the specific set of materials used to derive it. It may not be accurate for materials with different compositions or microstructures.
- Scale Non-Linearity: The Mohs scale is non-linear, and the relationship between Mohs hardness and metal hardness may not be linear either. This can lead to inaccuracies in the correlation.
- Environmental Factors: The correlation may be affected by environmental factors such as temperature, humidity, and the presence of surface contaminants.
4.2. Conversion Charts
Conversion charts provide a tabular representation of the approximate relationship between different hardness scales. These charts are typically based on empirical correlations or data from various sources and provide a quick way to estimate the equivalent hardness value in another scale.
However, conversion charts should be used with caution due to their inherent limitations:
- Approximation: Conversion charts provide only approximate values, and the actual hardness may vary depending on the material and testing conditions.
- Limited Range: Conversion charts may only cover a limited range of hardness values, and extrapolation beyond this range can lead to significant errors.
- Material Specificity: Conversion charts are often based on specific materials and may not be accurate for other materials.
4.3. Challenges and Limitations in Conversion
Several challenges and limitations arise when attempting to convert between metal and mineral hardness scales:
- Different Measurement Principles: Metal hardness tests measure resistance to indentation, while the Mohs scale measures resistance to scratching. These are fundamentally different properties, and there is no direct theoretical relationship between them.
- Scale Types: Metal hardness tests provide quantitative, interval, or ratio scale measurements, while the Mohs scale is a qualitative, ordinal scale. Converting between these scale types is inherently problematic.
- Material Properties: Metals and minerals have distinct material properties, such as ductility, malleability, and anisotropy. These differences can affect the hardness measurements and make conversion difficult.
- Lack of Standardization: There is no standardized method for converting between metal and mineral hardness scales, and different correlations and conversion charts may provide different results.
This rough diamond shows its octahedral cleavage.
5. Practical Applications and Considerations
5.1. Selecting Materials Based on Hardness
When selecting materials for engineering applications, hardness is often a critical consideration. However, the specific hardness requirements depend on the application’s nature and the expected loading conditions.
- Wear Resistance: For applications where wear resistance is important, such as cutting tools, bearings, and gears, materials with high hardness are typically preferred. Hard materials can resist abrasion, erosion, and other forms of wear, extending the component’s service life.
- Indentation Resistance: For applications where indentation resistance is important, such as armor plating, protective coatings, and structural components, materials with high hardness are also preferred. Hard materials can resist penetration by foreign objects, protecting the underlying structure.
- Scratch Resistance: For applications where scratch resistance is important, such as optical lenses, display screens, and decorative surfaces, materials with high hardness are desirable. Hard materials can resist scratching, maintaining the appearance and functionality of the component.
5.2. Case Studies: Hardness in Different Industries
- Mining Industry: In the mining industry, hardness is a critical factor in selecting materials for drilling, crushing, and grinding equipment. Hard minerals like quartz and corundum can cause significant wear on mining equipment, so materials with high hardness and wear resistance are essential. For example, tungsten carbide composites are often used in drill bits and crushing hammers due to their extreme hardness and abrasion resistance.
- Aerospace Industry: In the aerospace industry, hardness is important for selecting materials for turbine blades, landing gear, and other critical components. These components are subjected to high stresses and temperatures, so materials with high hardness and strength are required. For example, titanium alloys and nickel-based superalloys are often used in aerospace applications due to their high hardness and strength-to-weight ratio.
- Automotive Industry: In the automotive industry, hardness is important for selecting materials for engine components, gears, and bearings. These components are subjected to high stresses and temperatures, so materials with high hardness and wear resistance are required. For example, hardened steel and cast iron are commonly used in automotive applications due to their high hardness and wear resistance.
- Jewelry Industry: In the jewelry industry, hardness is a key factor in selecting gemstones for rings, necklaces, and other adornments. Hard gemstones like diamonds, sapphires, and rubies are preferred because they are resistant to scratching and wear, maintaining their brilliance and beauty over time.
5.3. The Role of Hardness Testing in Quality Control
Hardness testing plays a crucial role in quality control processes across various industries. By measuring the hardness of materials, manufacturers can ensure that their products meet the required specifications and performance standards.
- Material Verification: Hardness testing can be used to verify the composition and heat treatment of materials. For example, if a steel component is supposed to be hardened to a specific hardness range, hardness testing can be used to confirm that the heat treatment process was successful.
- Process Monitoring: Hardness testing can be used to monitor the consistency of manufacturing processes. For example, if a machine is producing parts with varying hardness values, hardness testing can be used to identify and correct the problem.
- Product Inspection: Hardness testing can be used to inspect finished products for defects. For example, if a product is supposed to have a specific hardness value, hardness testing can be used to identify and reject defective products.
Sheets of mica.
6. New Trends and Technologies in Hardness Measurement
6.1. Instrumented Indentation Testing (IIT)
Instrumented Indentation Testing (IIT), also known as nanoindentation or microindentation, is an advanced technique for measuring the mechanical properties of materials at small scales. Unlike traditional hardness tests, IIT continuously monitors the force and displacement during indentation, providing detailed information about the material’s elastic and plastic behavior.
IIT involves pressing an indenter into the material’s surface and measuring the force and displacement as a function of time. The resulting force-displacement curve can be used to determine various material properties, including hardness, elastic modulus, yield strength, and creep resistance.
6.2. Ultrasonic Contact Impedance (UCI) Method
The Ultrasonic Contact Impedance (UCI) method is a non-destructive technique for measuring the hardness of materials. The UCI method involves pressing an oscillating rod with a Vickers diamond indenter against the material’s surface. The frequency of the ultrasonic oscillations changes depending on the contact area between the indenter and the material. The change in frequency is then correlated to the material’s hardness.
The UCI method offers several advantages over traditional hardness tests:
- Non-Destructive: The UCI method is non-destructive and leaves only a small, shallow indentation on the material’s surface.
- Portable: UCI hardness testers are typically portable and can be used in the field.
- Fast Measurement: The UCI method provides a fast measurement of hardness.
6.3. Advanced Data Analysis and Machine Learning
Advanced data analysis techniques, such as machine learning, are increasingly being used to enhance hardness testing. Machine learning algorithms can be trained to analyze hardness data and predict material properties, identify defects, and optimize manufacturing processes.
- Predictive Modeling: Machine learning models can be trained to predict material properties based on hardness data and other input variables. This can be used to reduce the amount of testing required and accelerate material development.
- Defect Detection: Machine learning algorithms can be used to identify defects in materials based on hardness data. This can be used to improve quality control and prevent failures.
- Process Optimization: Machine learning models can be used to optimize manufacturing processes based on hardness data. This can be used to improve efficiency and reduce costs.
Chrysotile has splintery fracture.
7. Conclusion: Hardness as a Key Material Property
In conclusion, while comparing metal and mineral hardness requires careful consideration of the measurement methods and scale types, hardness remains a crucial property for selecting materials in various applications. Metal hardness is typically measured using indentation tests like Rockwell, Vickers, and Brinell, while mineral hardness is assessed using the Mohs scale, which measures scratch resistance.
Direct comparison between these scales is challenging due to their fundamental differences. However, empirical correlations and conversion charts can provide approximate relationships between them. When selecting materials, it’s essential to consider the specific hardness requirements of the application, as well as other factors like wear resistance, indentation resistance, and scratch resistance. Hardness testing plays a critical role in quality control, ensuring that materials meet the required specifications and performance standards.
New trends and technologies, such as Instrumented Indentation Testing (IIT), Ultrasonic Contact Impedance (UCI), and advanced data analysis techniques, are enhancing hardness measurement and providing more detailed information about material properties. By understanding the nuances of hardness measurement and considering the specific requirements of each application, engineers and designers can make informed decisions and select materials that provide optimal performance and durability.
Confused about which material is best for your project? Visit COMPARE.EDU.VN for detailed comparisons and expert advice to help you make the right choice.
Address: 333 Comparison Plaza, Choice City, CA 90210, United States
Whatsapp: +1 (626) 555-9090
Website: compare.edu.vn
8. FAQ
1. What is the difference between hardness and toughness?
Hardness measures a material’s resistance to localized plastic deformation, such as indentation or scratching, while toughness measures a material’s resistance to fracture when subjected to impact or stress. A hard material is resistant to surface deformation, whereas a tough material can absorb energy and resist crack propagation.
2. Can the Mohs scale be used to measure the hardness of metals?
The Mohs scale is primarily designed for minerals and is not suitable for measuring the hardness of metals. Metal hardness is typically measured using indentation tests like Rockwell, Vickers, or Brinell.
3. Is diamond the hardest material in the universe?
Diamond is the hardest naturally occurring material known to humans. However, some synthetic materials, such as aggregated diamond nanorods, are even harder than diamond.
4. How is hardness affected by temperature?
Generally, the hardness of most materials decreases with increasing temperature. At higher temperatures, the atoms in the material have more thermal energy, making it easier for them to move and deform.
5. What is the Knoop hardness test?
The Knoop hardness test is a microhardness test that uses a diamond indenter with an elongated pyramidal shape to create a shallow indentation. The Knoop hardness number is calculated based on the length of the long diagonal of the indentation. It is useful for measuring the hardness of brittle materials and thin coatings.
6. How does the grain size of a metal affect its hardness?
Generally, metals with smaller grain sizes tend to be harder than metals with larger grain sizes. This is because smaller grains provide more grain boundaries, which impede the movement of dislocations and increase the material’s resistance to deformation.
7. What is work hardening?
Work hardening, also known as strain hardening or cold working, is the process of increasing a metal’s hardness and strength by plastically deforming it at room temperature. During work hardening, dislocations are generated and entangled, making it more difficult for them to move and deform the material.
8. Can hardness be used to predict the wear resistance of a material?
Hardness is often used as an indicator of wear resistance, but it is not the only factor. Other factors, such as the material’s composition, microstructure, and the nature of the wear environment, also play a significant role.
9. What are some common applications of hard coatings?
Hard coatings are used in various applications to improve wear resistance, corrosion resistance, and other properties. Some common applications include cutting tools, bearings, gears, and decorative surfaces.
10. How is the hardness of a composite material determined?
The hardness of a composite material depends on the hardness of its constituent materials and their volume fractions. The overall hardness of the composite can be estimated using rule-of-mixtures equations or measured experimentally using hardness tests.