Are carbon fiber more expensive compared to steel? Yes, carbon fiber generally has a higher price point than steel due to its complex manufacturing processes and high-performance qualities, but to make the right decision for your project, it’s important to consider the benefits and drawbacks of each material. At compare.edu.vn, we break down the key differences in cost, strength, weight, and applications to help you make an informed decision. Dive in to understand which material aligns best with your needs, considering factors such as material costs, fabrication, and long-term ownership expenses as well as the unique properties.
1. Understanding Carbon Fiber and Steel
To effectively compare carbon fiber and steel, it is essential to first understand what each material entails and their distinct properties. This involves examining their composition, manufacturing processes, and inherent characteristics that dictate their suitability for various applications.
1.1. Carbon Fiber: Composition, Manufacturing, and Characteristics
Carbon fiber is a composite material crafted from thin strands of carbon atoms intricately woven together and then bonded with a resin matrix. This material is known for its high strength-to-weight ratio. The carbon fibers themselves are produced through a process called pyrolysis, where organic precursor fibers, such as polyacrylonitrile (PAN), pitch, or rayon, are heated to high temperatures in an inert atmosphere. This process carbonizes the fibers, leaving behind a structure composed mainly of carbon atoms aligned along the fiber’s axis.
The resultant carbon fibers are exceptionally strong and stiff. However, they are also brittle and need to be embedded in a matrix material, typically a polymer resin like epoxy, polyester, or vinyl ester, to form a composite. This matrix protects the fibers from damage and transfers loads between them, enhancing the overall strength and durability of the composite material. The manufacturing process involves several steps, including:
- Fiber Production: Creating the carbon fibers through pyrolysis.
- Weaving or Laying: Arranging the fibers into a fabric or specific orientation.
- Resin Infusion: Impregnating the fibers with resin.
- Curing: Hardening the resin to form a solid composite.
Carbon fiber composites exhibit several key characteristics:
- High Strength-to-Weight Ratio: One of the most significant advantages, offering substantial strength at a fraction of the weight of steel.
- Stiffness: Carbon fiber is exceptionally stiff, providing excellent rigidity and dimensional stability.
- Corrosion Resistance: Unlike steel, carbon fiber is highly resistant to corrosion from moisture, chemicals, and other environmental factors.
- Fatigue Resistance: Carbon fiber can withstand repeated stress cycles without significant degradation, making it suitable for applications involving cyclic loading.
- Thermal Conductivity: Carbon fiber has low thermal conductivity, making it useful in applications requiring thermal insulation.
- Electrical Conductivity: Depending on the type and orientation of the fibers, carbon fiber can be electrically conductive, which can be both an advantage and a disadvantage depending on the application.
1.2. Steel: Composition, Manufacturing, and Characteristics
Steel is an alloy primarily composed of iron and carbon, with small amounts of other elements such as manganese, silicon, and chromium to impart specific properties. The manufacturing process begins with the extraction of iron ore, which is then smelted in a blast furnace to produce molten iron. This molten iron is further refined to remove impurities and adjust the carbon content to the desired level.
The steel is then shaped through various processes, including:
- Casting: Pouring molten steel into molds to create specific shapes.
- Rolling: Passing steel through rollers to reduce its thickness and increase its length.
- Forging: Shaping steel using compressive forces.
- Extrusion: Forcing steel through a die to create complex cross-sectional shapes.
Steel comes in various types and grades, each with distinct properties:
- Carbon Steel: Primarily iron and carbon, with varying carbon content affecting its hardness and weldability.
- Alloy Steel: Contains additional elements like manganese, silicon, nickel, chromium, vanadium, and molybdenum to enhance strength, toughness, corrosion resistance, and other properties.
- Stainless Steel: Contains a high percentage of chromium (typically 10.5% or more), providing excellent corrosion resistance.
- Tool Steel: High-hardness steels used for cutting, shaping, and forming other materials.
Key characteristics of steel include:
- High Strength: Steel is known for its high tensile and compressive strength, making it suitable for load-bearing applications.
- Durability: Steel is a durable material that can withstand harsh conditions and wear.
- Stiffness: Steel has high stiffness, providing rigidity and resistance to deformation.
- Weldability: Many types of steel can be easily welded, facilitating fabrication and construction.
- Cost-Effectiveness: Steel is generally more affordable than carbon fiber, especially for large-scale applications.
- Recyclability: Steel is highly recyclable, making it an environmentally friendly choice.
- Corrosion Susceptibility: Steel is prone to corrosion, especially in humid or marine environments, unless it is treated or alloyed with corrosion-resistant elements like chromium.
Understanding these fundamental aspects of carbon fiber and steel provides a solid foundation for comparing their properties and cost-effectiveness in various applications.
2. Cost Analysis: Carbon Fiber vs. Steel
When evaluating materials for a project, cost is often a primary consideration. Both the initial material cost and the long-term expenses associated with fabrication, maintenance, and lifespan play crucial roles in making an informed decision. This section provides a detailed cost analysis comparing carbon fiber and steel across these critical factors.
2.1. Material Costs
The raw material cost is a significant factor in the overall expense of a project. Carbon fiber, known for its exceptional properties, typically comes with a higher price tag compared to steel.
Carbon Fiber: The cost of carbon fiber is influenced by several factors, including the type of fiber, the resin used in the composite, and the manufacturing process. High-grade carbon fibers, which offer superior strength and stiffness, are more expensive. Additionally, specialized resins and advanced manufacturing techniques can further increase the material cost.
Steel: Steel is generally more affordable than carbon fiber due to the abundance of iron ore and well-established manufacturing processes. The cost of steel varies depending on the grade, alloy composition, and market demand. However, even high-strength steel alloys tend to be less expensive than comparable carbon fiber composites.
Comparative Cost: On average, carbon fiber can be several times more expensive than steel on a per-pound or per-kilogram basis. This cost difference is primarily attributed to the energy-intensive manufacturing processes and the specialized materials required to produce high-quality carbon fiber composites.
2.2. Fabrication Costs
Fabrication costs encompass all expenses related to transforming raw materials into finished components. These costs include labor, equipment, energy, and any specialized processes required for each material.
Carbon Fiber: Fabricating with carbon fiber can be labor-intensive and requires skilled technicians. The process often involves:
- Layup: Precisely layering carbon fiber sheets into a mold.
- Resin Infusion: Ensuring the resin is evenly distributed throughout the fiber layers.
- Curing: Applying heat and pressure to harden the composite.
- Finishing: Trimming, sanding, and applying coatings to achieve the desired surface finish.
These steps necessitate specialized equipment such as autoclaves, vacuum pumps, and precision cutting tools. Additionally, the cost of tooling and molds for carbon fiber components can be substantial, particularly for complex shapes.
Steel: Steel fabrication is a well-established process with a wide range of techniques available, including:
- Cutting: Using saws, lasers, or plasma cutters to shape steel plates and profiles.
- Welding: Joining steel components using various welding methods.
- Machining: Precisely shaping steel parts using milling, turning, and drilling operations.
- Forming: Bending, stamping, or pressing steel into desired shapes.
Steel fabrication benefits from economies of scale, with numerous service providers and standardized processes that help reduce costs. The equipment required for steel fabrication is generally less expensive and more readily available than that for carbon fiber.
Comparative Cost: The fabrication costs for carbon fiber are typically higher than those for steel. The labor-intensive nature of carbon fiber fabrication, coupled with the need for specialized equipment and tooling, contributes to this cost difference.
2.3. Long-Term Costs: Maintenance and Lifespan
Long-term costs associated with maintenance and lifespan are crucial for evaluating the overall cost-effectiveness of a material. These costs include expenses related to repairs, replacements, and preventive measures to ensure the material performs optimally over its service life.
Carbon Fiber: Carbon fiber composites are known for their exceptional durability and corrosion resistance. They are less susceptible to rust and degradation from environmental factors compared to steel. This results in lower maintenance costs and extended lifespans in many applications. However, carbon fiber can be vulnerable to impact damage, which may require specialized repairs.
Steel: Steel is prone to corrosion, particularly in humid or marine environments. Regular maintenance, such as painting or applying protective coatings, is necessary to prevent rust and degradation. While steel is highly durable, it may require more frequent repairs or replacements compared to carbon fiber, especially in corrosive environments.
Comparative Cost: While carbon fiber may have higher initial costs, its lower maintenance requirements and longer lifespan can lead to reduced long-term costs in certain applications. Steel, on the other hand, may have lower upfront costs but higher maintenance expenses over time.
2.4. Total Cost of Ownership
To provide a comprehensive comparison, it is essential to consider the total cost of ownership, which includes material costs, fabrication costs, and long-term maintenance expenses.
Carbon Fiber:
- Pros:
- High strength-to-weight ratio
- Excellent corrosion resistance
- Long lifespan
- Lower maintenance costs
- Cons:
- High initial material cost
- Expensive fabrication process
- Vulnerable to impact damage
Steel:
- Pros:
- Lower initial material cost
- Established fabrication methods
- High strength and durability
- Cons:
- Susceptible to corrosion
- Requires regular maintenance
- Heavier than carbon fiber
Comparative Analysis: In applications where weight reduction and corrosion resistance are critical, carbon fiber may prove to be more cost-effective over the long term, despite its higher upfront costs. Conversely, steel may be a more economical choice for projects where budget constraints are a primary concern and weight or corrosion resistance are not critical factors.
Ultimately, the choice between carbon fiber and steel depends on a careful evaluation of project requirements, budget limitations, and long-term performance goals.
3. Strength and Weight: A Comparative Analysis
When selecting a material for any application, strength and weight are two of the most critical factors to consider. The strength-to-weight ratio of a material determines its efficiency in load-bearing applications and its impact on overall system performance. This section provides a detailed comparison of the strength and weight characteristics of carbon fiber and steel.
3.1. Strength Comparison
Strength refers to a material’s ability to withstand stress without breaking or deforming. It is typically measured in terms of tensile strength (resistance to pulling forces), compressive strength (resistance to crushing forces), and flexural strength (resistance to bending forces).
Carbon Fiber: Carbon fiber composites are renowned for their exceptional tensile strength. High-grade carbon fibers can have a tensile strength of up to 7 GPa (gigapascals), which is significantly higher than that of most steel alloys. However, carbon fiber is generally weaker in compression and shear compared to steel. The strength of carbon fiber composites is highly dependent on the orientation of the fibers and the quality of the resin matrix.
Steel: Steel exhibits high tensile and compressive strength, making it suitable for a wide range of structural applications. High-strength steel alloys can have tensile strengths ranging from 0.4 to 2.0 GPa, depending on the composition and heat treatment. Steel is particularly strong in compression, making it an excellent choice for applications involving compressive loads.
Comparative Analysis:
- Tensile Strength: Carbon fiber generally outperforms steel in tensile strength, making it ideal for applications where resistance to pulling forces is critical.
- Compressive Strength: Steel typically has higher compressive strength than carbon fiber, making it better suited for applications involving crushing forces.
- Flexural Strength: The flexural strength of both materials depends on the specific composition and manufacturing process. However, carbon fiber composites can be tailored to achieve high flexural strength by optimizing the fiber orientation and resin matrix.
3.2. Weight Comparison
Weight is another critical factor to consider, particularly in applications where minimizing mass is essential, such as aerospace, automotive, and sports equipment.
Carbon Fiber: Carbon fiber composites are exceptionally lightweight, with a density of approximately 1.6 to 2.0 g/cm3. This is significantly lower than the density of steel, which ranges from 7.8 to 8.0 g/cm3. The low density of carbon fiber allows for substantial weight savings compared to steel, without sacrificing strength.
Steel: Steel is a relatively heavy material due to its high density. While the high strength of steel allows for the use of thinner sections in some applications, the overall weight of steel components tends to be higher than that of comparable carbon fiber components.
Comparative Analysis:
- Density: Carbon fiber is significantly less dense than steel, resulting in lighter components.
- Weight Savings: The use of carbon fiber can reduce the weight of a component by as much as 70% compared to steel.
3.3. Strength-to-Weight Ratio
The strength-to-weight ratio is a key metric for evaluating the efficiency of a material in load-bearing applications. It is calculated by dividing the material’s strength by its density.
Carbon Fiber: Carbon fiber composites have an exceptionally high strength-to-weight ratio due to their high strength and low density. This makes them ideal for applications where maximizing strength while minimizing weight is critical.
Steel: Steel has a lower strength-to-weight ratio compared to carbon fiber, although it is still a respectable material for many structural applications. The high density of steel reduces its strength-to-weight ratio relative to carbon fiber.
Comparative Analysis:
- Efficiency: Carbon fiber is more efficient than steel in load-bearing applications due to its higher strength-to-weight ratio.
- Performance: The use of carbon fiber can improve the performance of systems by reducing weight, increasing speed, and enhancing fuel efficiency.
3.4. Practical Implications
The strength and weight characteristics of carbon fiber and steel have significant implications for various applications:
- Aerospace: Carbon fiber is widely used in aircraft components such as wings, fuselages, and control surfaces to reduce weight, improve fuel efficiency, and enhance performance.
- Automotive: Carbon fiber is increasingly used in automotive components such as body panels, chassis, and suspension parts to reduce weight, improve handling, and enhance fuel economy.
- Sports Equipment: Carbon fiber is used in sports equipment such as bicycles, tennis rackets, and golf clubs to improve performance and reduce weight.
- Construction: Steel is widely used in construction for structural components such as beams, columns, and reinforcing bars due to its high strength and cost-effectiveness.
In summary, carbon fiber offers superior tensile strength and a significantly higher strength-to-weight ratio compared to steel. While steel has higher compressive strength and is more cost-effective, carbon fiber is the preferred choice for applications where weight reduction and high performance are paramount.
.png)
4. Durability and Corrosion Resistance
Durability and corrosion resistance are essential considerations when selecting materials for engineering applications, especially in harsh environments. These factors directly impact the lifespan, maintenance requirements, and overall cost-effectiveness of a component or structure. This section provides a detailed comparison of the durability and corrosion resistance of carbon fiber and steel.
4.1. Durability Comparison
Durability refers to a material’s ability to withstand wear, abrasion, impact, and other forms of degradation over time. It is a critical factor in determining the longevity and reliability of a component or structure.
Carbon Fiber: Carbon fiber composites exhibit excellent fatigue resistance, meaning they can withstand repeated cycles of stress without significant degradation. They are also resistant to many forms of chemical attack, making them suitable for use in corrosive environments. However, carbon fiber can be vulnerable to impact damage, particularly from sharp objects or high-energy impacts.
Steel: Steel is a durable material with high resistance to wear and abrasion. It can withstand significant loads and impacts without fracturing. However, steel is susceptible to fatigue failure, especially under cyclic loading conditions. The durability of steel can be improved through heat treatment and alloying with other elements.
Comparative Analysis:
- Fatigue Resistance: Carbon fiber generally outperforms steel in fatigue resistance, making it ideal for applications involving cyclic loading.
- Wear Resistance: Steel typically has higher wear resistance than carbon fiber, making it better suited for applications involving abrasion or friction.
- Impact Resistance: Steel is more resistant to impact damage than carbon fiber, although the impact resistance of carbon fiber composites can be improved through the use of toughened resins and fiber architectures.
4.2. Corrosion Resistance Comparison
Corrosion is the degradation of a material due to chemical or electrochemical reactions with its environment. It is a significant concern for many engineering applications, especially those exposed to moisture, salt, or other corrosive substances.
Carbon Fiber: Carbon fiber composites are highly resistant to corrosion due to the inert nature of the carbon fibers and the protective properties of the resin matrix. They do not rust or degrade in the presence of moisture, salt, or many chemicals. This makes carbon fiber an excellent choice for applications in marine, aerospace, and chemical processing environments.
Steel: Steel is susceptible to corrosion, particularly in humid or marine environments. It can rust and degrade over time, leading to structural failure and reduced service life. The corrosion resistance of steel can be improved through the use of protective coatings such as paint, galvanizing, or powder coating. Stainless steel alloys, which contain a high percentage of chromium, offer excellent corrosion resistance but are more expensive than carbon steel.
Comparative Analysis:
- Resistance to Rust: Carbon fiber is completely resistant to rust, while steel is prone to rusting unless properly protected.
- Resistance to Chemical Attack: Carbon fiber is resistant to many chemicals, while steel can be corroded by acids, bases, and other corrosive substances.
- Performance in Harsh Environments: Carbon fiber performs exceptionally well in harsh environments due to its corrosion resistance, while steel requires regular maintenance and protection to prevent corrosion.
4.3. Practical Implications
The durability and corrosion resistance characteristics of carbon fiber and steel have significant implications for various applications:
- Marine: Carbon fiber is used in boat hulls, decks, and other marine components due to its corrosion resistance and lightweight properties.
- Aerospace: Carbon fiber is used in aircraft structures to reduce weight and improve corrosion resistance, especially in environments with high humidity and salt exposure.
- Chemical Processing: Carbon fiber is used in chemical processing equipment such as tanks, pipes, and reactors due to its resistance to chemical attack.
- Infrastructure: Steel is used in bridges, buildings, and other infrastructure projects, but it requires regular maintenance and protection to prevent corrosion.
In summary, carbon fiber offers superior corrosion resistance and excellent fatigue resistance compared to steel. While steel is more resistant to wear and impact damage, its susceptibility to corrosion makes it less durable in many environments. The choice between carbon fiber and steel depends on the specific application requirements and the environmental conditions to which the material will be exposed.
5. Applications of Carbon Fiber and Steel
The unique properties of carbon fiber and steel make them suitable for a wide range of applications across various industries. Understanding where each material excels can help in making informed decisions for specific engineering and design needs. This section outlines the primary applications of both carbon fiber and steel, highlighting their respective advantages in each context.
5.1. Applications of Carbon Fiber
Carbon fiber composites are utilized in applications that require high strength-to-weight ratio, stiffness, and corrosion resistance. Here are some key applications:
- Aerospace Industry:
- Aircraft Structures: Wings, fuselages, control surfaces, and interior components.
- Spacecraft Components: Satellite structures, rocket motor cases, and heat shields.
Advantages:
-
Weight reduction leading to improved fuel efficiency.
-
High stiffness enhancing aerodynamic performance.
-
Corrosion resistance reducing maintenance costs.
-
Automotive Industry:
- High-Performance Vehicles: Body panels, chassis, and interior components in sports cars and racing vehicles.
- Electric Vehicles: Battery enclosures and structural components.
Advantages:
-
Weight reduction improving vehicle performance and fuel economy.
-
Enhanced safety due to high strength and impact resistance.
-
Increased design flexibility.
-
Sports Equipment:
- Bicycles: Frames, forks, handlebars, and seat posts.
- Tennis Rackets: Frames providing stiffness and power.
- Golf Clubs: Shafts for increased swing speed and accuracy.
- Fishing Rods: Blanks offering sensitivity and strength.
Advantages:
-
Lightweight design enhancing athletic performance.
-
High stiffness improving power transfer.
-
Customizable designs for specific sports requirements.
-
Renewable Energy:
- Wind Turbine Blades: Large blades that capture wind energy.
Advantages:
-
High strength-to-weight ratio enabling larger blade designs.
-
Fatigue resistance ensuring long-term reliability.
-
Medical Equipment:
- Prosthetics: Lightweight and strong artificial limbs.
- Medical Imaging Equipment: Components requiring high stiffness and dimensional stability.
Advantages:
- Lightweight design improving patient comfort and mobility.
- High strength ensuring structural integrity.
5.2. Applications of Steel
Steel is widely used in applications that require high strength, durability, and cost-effectiveness. Here are some key applications:
- Construction Industry:
- Structural Framework: Beams, columns, and reinforcing bars in buildings and bridges.
Advantages:
-
High strength providing structural integrity.
-
Cost-effectiveness for large-scale projects.
-
Ease of fabrication and installation.
-
Automotive Industry:
- Vehicle Frames and Chassis: Structural components providing safety and stability.
- Body Panels: Exterior panels providing protection and aesthetics.
Advantages:
-
High strength ensuring vehicle safety.
-
Cost-effectiveness for mass production.
-
Good formability for complex shapes.
-
Manufacturing Industry:
- Machinery and Equipment: Components in industrial machinery.
- Tools and Dies: High-hardness steels used for cutting, shaping, and forming.
Advantages:
-
High strength and durability for demanding applications.
-
Good machinability and formability.
-
Transportation:
- Railways: Rails, wheels, and structural components in trains.
- Shipping: Hulls and structural components in ships.
Advantages:
-
High strength ensuring safety and reliability.
-
Cost-effectiveness for large-scale infrastructure.
-
Consumer Goods:
- Appliances: Structural components in refrigerators, washing machines, and ovens.
- Furniture: Frames and supports in chairs, tables, and beds.
Advantages:
- High strength and durability for long-lasting products.
- Cost-effectiveness for mass production.
5.3. Comparative Analysis
Feature | Carbon Fiber | Steel |
---|---|---|
Strength-to-Weight | Very High | Moderate |
Corrosion Resistance | Excellent | Poor (unless treated or alloyed) |
Stiffness | High | High |
Durability | Good (except impact resistance) | Good |
Cost | High | Low |
Applications | Aerospace, Automotive (high-performance), Sports Equipment, Renewable Energy, Medical Equipment | Construction, Automotive, Manufacturing, Transportation, Consumer Goods |
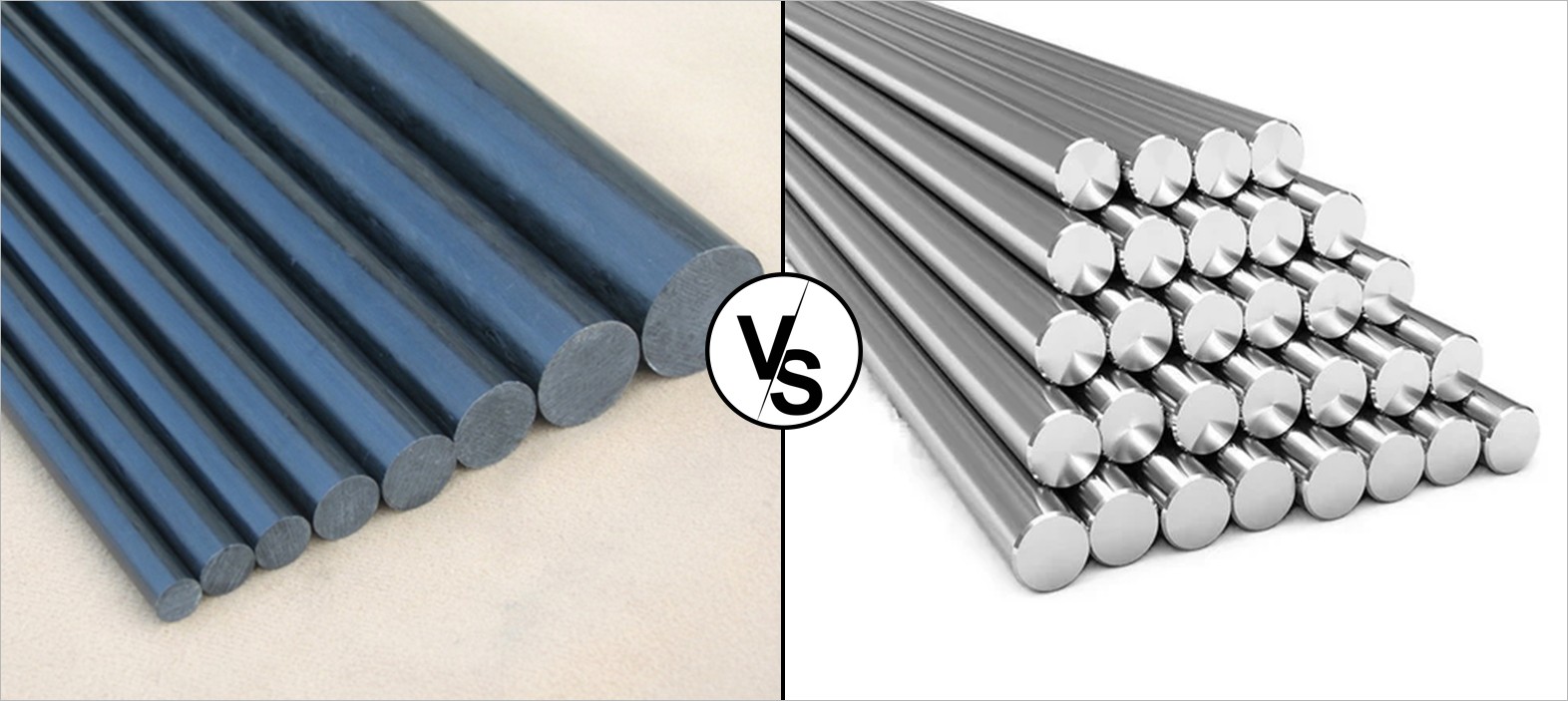
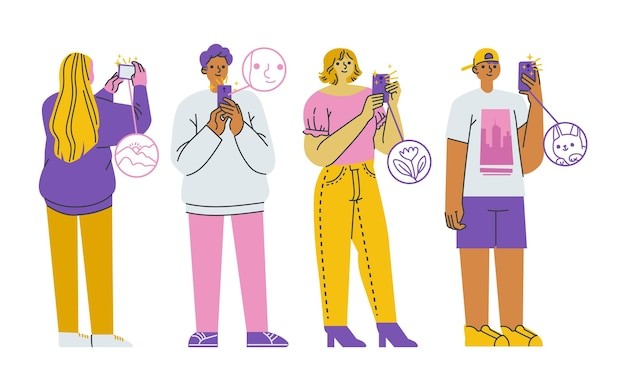
In summary, carbon fiber is preferred in applications where weight reduction, high stiffness, and corrosion resistance are critical, despite its higher cost. Steel is favored in applications where high strength, durability, and cost-effectiveness are paramount, even if it means dealing with greater weight and potential corrosion issues.
6. Factors Influencing Material Selection
Selecting the right material for a project requires a comprehensive evaluation of various factors that go beyond just cost and strength. The decision-making process should consider performance requirements, environmental conditions, manufacturing capabilities, and long-term implications. This section outlines the critical factors that influence the selection of carbon fiber and steel.
6.1. Performance Requirements
The required performance characteristics of the final product are paramount in material selection. Key considerations include:
- Strength and Stiffness: The material must withstand the anticipated loads and maintain its shape under stress. If high strength-to-weight ratio is essential, carbon fiber is often preferred.
- Weight: In applications where minimizing weight is critical, such as aerospace and high-performance vehicles, carbon fiber offers a significant advantage.
- Durability: The material must withstand wear, abrasion, and fatigue over its intended lifespan. Steel is generally more resistant to wear, while carbon fiber excels in fatigue resistance.
- Impact Resistance: The ability to withstand sudden impacts without fracturing is crucial in many applications. Steel generally offers better impact resistance than carbon fiber.
- Thermal Properties: The material’s behavior under varying temperatures, including thermal expansion and conductivity, must be considered.
- Vibration Damping: The material’s ability to dampen vibrations can be important in applications where noise and vibration control are necessary.
6.2. Environmental Conditions
The environmental conditions to which the material will be exposed significantly influence its performance and longevity. Key considerations include:
- Corrosion Resistance: In marine, chemical processing, and outdoor environments, corrosion resistance is crucial. Carbon fiber offers superior corrosion resistance compared to steel.
- Temperature: Extreme temperatures can affect the strength and stiffness of materials. The operating temperature range must be considered when selecting a material.
- UV Exposure: Prolonged exposure to ultraviolet (UV) radiation can degrade certain materials. Protective coatings may be necessary to mitigate UV damage.
- Chemical Exposure: Exposure to chemicals can cause corrosion or degradation of materials. Chemical resistance must be considered when selecting a material for chemical processing applications.
6.3. Manufacturing Capabilities
The available manufacturing processes and equipment can influence the choice of material. Key considerations include:
- Fabrication Techniques: The material must be compatible with available fabrication techniques such as machining, welding, molding, and forming.
- Tooling Costs: The cost of tooling and molds can vary significantly between materials. Carbon fiber often requires more expensive tooling than steel.
- Production Volume: The production volume can affect the cost-effectiveness of different materials. Steel benefits from economies of scale in high-volume production.
- Labor Costs: The labor costs associated with fabrication can vary depending on the material and the complexity of the manufacturing process. Carbon fiber fabrication often requires skilled technicians and is more labor-intensive than steel fabrication.
6.4. Cost Considerations
Cost is always a significant factor in material selection. Key considerations include:
- Material Costs: The raw material cost can vary significantly between materials. Steel is generally more affordable than carbon fiber.
- Fabrication Costs: The cost of transforming raw materials into finished components must be considered. Carbon fiber fabrication is often more expensive than steel fabrication.
- Maintenance Costs: The long-term maintenance costs associated with repairs, replacements, and preventive measures must be factored in. Carbon fiber may have lower maintenance costs due to its corrosion resistance.
- Lifespan Costs: The expected lifespan of the component or structure must be considered. Carbon fiber may offer a longer lifespan in certain applications due to its durability and corrosion resistance.
6.5. Sustainability
Sustainability is an increasingly important factor in material selection. Key considerations include:
- Recyclability: The ability to recycle the material at the end of its service life is desirable. Steel is highly recyclable, while carbon fiber recycling is more challenging.
- Environmental Impact: The environmental impact of producing and processing the material must be considered.
- Energy Consumption: The energy consumed during the manufacturing process is a factor. Steel production is energy-intensive, while carbon fiber production requires even more energy.
- Waste Generation: The amount of waste generated during manufacturing should be minimized.
By carefully evaluating these factors, engineers and designers can make informed decisions about whether to use carbon fiber or steel for a specific application.
7. Case Studies: Comparing Applications
To further illustrate the differences and trade-offs between carbon fiber and steel, it is helpful to examine specific case studies where these materials are used. This section presents several case studies highlighting the applications, advantages, and disadvantages of each material in real-world scenarios.
7.1. Case Study 1: Automotive Industry – Body Panels
- Application: Body panels for automobiles.
- Material Options: Carbon Fiber vs. Steel.
Steel:
-
Advantages:
- High strength and impact resistance ensuring passenger safety.
- Cost-effectiveness for mass production.
- Well-established manufacturing processes.
-
Disadvantages:
- High weight reducing fuel efficiency.
- Susceptibility to corrosion requiring protective coatings.
Carbon Fiber:
-
Advantages:
- Significant weight reduction improving fuel efficiency and handling.
- High stiffness enhancing vehicle performance.
- Corrosion resistance reducing maintenance costs.
-
Disadvantages:
- High material and fabrication costs.
- Lower impact resistance compared to steel.
- Complex manufacturing processes.
Outcome: High-end sports cars and luxury vehicles often use carbon fiber body panels to achieve superior performance and weight reduction. Mainstream vehicles typically use steel due to its cost-effectiveness and ease of manufacturing.
7.2. Case Study 2: Aerospace Industry – Aircraft Wings
- Application: Wings for commercial aircraft.
- Material Options: Carbon Fiber vs. Aluminum/Steel.
Aluminum/Steel:
-
Advantages:
- High strength and fatigue resistance ensuring structural integrity.
- Well-established manufacturing processes.
- Lower material and fabrication costs compared to carbon fiber.
-
Disadvantages:
- Higher weight compared to carbon fiber.
- Susceptibility to corrosion requiring regular maintenance.
Carbon Fiber:
-
Advantages:
- Significant weight reduction improving fuel efficiency and payload capacity.
- High stiffness enhancing aerodynamic performance.
- Corrosion resistance reducing maintenance costs.
-
Disadvantages:
- High material and fabrication costs.
- Complex manufacturing processes.
Outcome: Modern commercial aircraft increasingly use carbon fiber composite wings to reduce weight and improve fuel efficiency. The Boeing 787 Dreamliner and Airbus A350 XWB are prime examples of aircraft with extensive carbon fiber composite structures.
7.3. Case Study 3: Construction Industry – Bridge Structures
- Application: Structural components for bridge construction.
- Material Options: Steel vs. Carbon Fiber.
Steel:
-
Advantages:
- High strength and durability ensuring structural integrity.
- Cost-effectiveness for large-scale infrastructure projects.
- Well-established construction techniques.
-
Disadvantages:
- High weight requiring robust support structures.
- Susceptibility to corrosion requiring regular maintenance.
Carbon Fiber:
-
Advantages:
- Lightweight design reducing the load on support structures.
- High strength and stiffness enhancing structural performance.
- Corrosion resistance reducing maintenance costs.
-
Disadvantages:
- High material and fabrication costs.
- Complex construction techniques.
Outcome: Steel remains the primary material for bridge construction due to its cost-effectiveness and established construction techniques. Carbon fiber is used in niche applications such as cable-stayed bridges and bridge reinforcement to reduce weight and improve corrosion resistance.
7.4. Case Study 4: Sports Equipment – Bicycle Frames
- Application: Frames for high-performance bicycles.
- Material Options: Carbon Fiber vs. Aluminum/Steel.
Aluminum/Steel:
-
Advantages:
- High strength and durability ensuring rider safety.
- Cost-effectiveness for mass production.
- Well-established manufacturing processes.
-
Disadvantages:
- Higher weight compared to carbon fiber.
- Lower stiffness reducing power transfer efficiency.
Carbon Fiber:
-
Advantages:
- Significant weight reduction improving cycling performance.
- High stiffness enhancing power transfer efficiency.
- Customizable designs for specific riding styles.
-
Disadvantages:
- High material and fabrication costs.
- Lower impact resistance compared to aluminum/steel.
Outcome: High-end bicycles for professional cyclists and enthusiasts use carbon fiber frames to achieve superior performance and weight reduction. Aluminum and steel frames are common in more affordable bicycles for recreational use.
These case studies illustrate that the choice between carbon fiber and steel depends on a careful evaluation of application-specific requirements, performance goals, and cost constraints.
8. Future Trends in Material Science
The field of material science is continuously evolving, with ongoing research and development efforts focused on improving the properties, reducing the costs, and enhancing the sustainability of materials. This section explores the future trends in material science that are likely to impact the use of carbon fiber and steel in various applications.
8.1. Advancements in Carbon Fiber Technology
- Lower-Cost Carbon Fiber: Research is focused on developing lower-cost carbon fiber production methods to make the material more accessible for a wider range of applications. This includes exploring alternative precursor materials and reducing energy consumption during the manufacturing process.
- Improved Resin Systems: Development of advanced resin systems that offer enhanced toughness, impact resistance, and thermal stability. These improved resin systems will expand the range of applications for carbon fiber composites.
- Self-Healing Composites: Research into self-healing composites that can automatically repair damage, extending the lifespan and reducing maintenance costs of carbon fiber components.
- Recyclable Carbon Fiber: Development of methods for recycling carbon fiber composites to reduce waste and improve the sustainability of the material. This includes chemical recycling processes that can recover high-quality carbon fibers from composite waste.
- Nanomaterial-Enhanced Composites: Incorporation of nanomaterials such as carbon nanotubes and graphene to enhance the strength, stiffness, and electrical conductivity of carbon fiber composites.
8.2. Advancements in Steel Technology
- High-Strength Steel Alloys: Development of new high-strength steel alloys that offer improved strength-to-weight ratios and corrosion resistance. These alloys will enable the design of lighter and more durable steel structures.
- Advanced Coating Technologies: Development of advanced coating technologies that provide enhanced corrosion protection for steel structures. This includes self-healing coatings and nano-coatings that offer superior resistance to environmental degradation.
- Additive Manufacturing of Steel: Use of additive manufacturing (3D printing) to create complex steel components with customized properties. This will enable the production of high-performance steel parts with reduced material waste and manufacturing costs.
- Smart Steel Structures: Integration of sensors and monitoring systems into steel structures to detect damage, monitor stress levels, and predict maintenance needs. This will improve the safety and reliability of steel infrastructure.
- Green Steel Production: Development of sustainable steel production methods that reduce carbon emissions and minimize environmental impact. This includes the use of renewable energy sources and carbon capture technologies.
8.3. Hybrid Materials and Structures
- Combining Carbon Fiber and Steel: Development of hybrid materials and structures that combine the advantages of both carbon fiber and steel. This includes using carbon fiber composites to reinforce steel structures and reduce weight, while leveraging the cost-effectiveness and impact resistance of steel in critical areas.
- Multi-Material Design Optimization: Use of advanced design optimization techniques to create multi-material structures that maximize performance while minimizing weight and cost. This involves carefully selecting and combining different materials to achieve the desired properties.
8.4. Digitalization and Automation
- Digital Twins: Use of digital twins to simulate the performance of materials and structures under various conditions, enabling engineers to optimize designs and predict maintenance needs.
- Automated Manufacturing: Implementation of automated manufacturing processes to reduce labor costs and improve the quality and consistency of carbon fiber and steel components. This includes the use of robotics, artificial intelligence, and machine learning